A Comprehensive Guide to Copper Machining Techniques
By:Admin
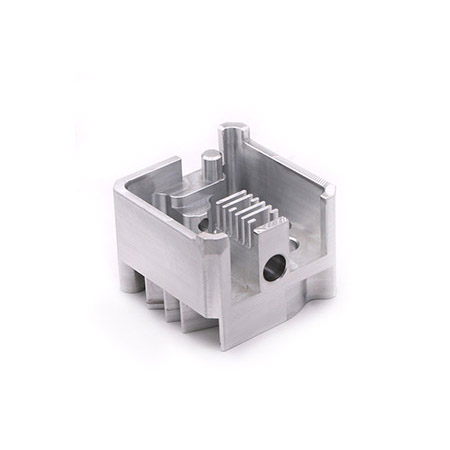
Introduction:
In today's rapidly evolving industrial landscape, precision is of paramount importance. The demand for high-quality and intricate components has never been higher, prompting manufacturers to explore advanced machining techniques. In response to this growing need, {Company Name}, a renowned leader in the manufacturing industry, is unveiling its latest innovation - Machining Copper 101. This groundbreaking solution promises to revolutionize the way copper components are manufactured, providing unprecedented precision and durability. Let us delve deep into the world of Machining Copper 101 and its implications for various industries.
I. Understanding Machining Copper 101:
Machining Copper 101 is a cutting-edge manufacturing technique developed by {Company Name}, harnessing the full potential of copper as a versatile material. With its refined composition and exceptional conductive properties, copper has long been the go-to material for electrical connectors, printed circuit boards, and various precision parts. However, its notoriously challenging nature when it comes to machining has always posed a hurdle for manufacturers seeking complex and highly accurate components. Enter Machining Copper 101 - a game-changer that bridges the gap between precision and copper manufacturing.
II. The Advantages of Machining Copper 101:
1. Unmatched Precision: Machining Copper 101 leverages state-of-the-art technology, enabling manufacturers to achieve sub-micron level precision. This breakthrough ensures tighter tolerances and increased reliability, meeting the ever-increasing demands of diverse industries.
2. Enhanced Efficiency: With Machining Copper 101, manufacturers can significantly reduce production time while maintaining impeccable quality. The optimized machining process eliminates the need for multiple operations, ultimately streamlining the manufacturing workflow.
3. Extended Durability: By employing Machining Copper 101, components gain enhanced durability and longevity. The method optimizes the microstructure of the copper, resulting in improved resistance to wear, corrosion, and mechanical stress, making it suitable for demanding applications.
4. Cost-effectiveness: The streamlined processes of Machining Copper 101 translate into reduced material waste, increased production throughput, and overall cost savings. Manufacturers can now provide superior products without compromising on profitability.
III. Applications across Industries:
The versatility of copper makes it a staple material across a wide range of industries. Machining Copper 101 opens up a plethora of options for manufacturers seeking to elevate their production standards in various sectors, including but not limited to:
1. Electronics: Copper is indispensable in manufacturing electronic components like connectors, heat sinks, and advanced electrical systems. Machining Copper 101 allows for intricate designs and higher contact densities, bolstering the performance of electronic devices.
2. Automotive: In the automotive sector, copper finds applications in wiring harnesses, sensors, brake systems, and engine components. With Machining Copper 101, manufacturers can create precise parts that ensure optimal functionality, efficiency, and safety.
3. Aerospace: The aerospace industry relies heavily on copper for critical applications such as aircraft wiring, connectors, and heat exchangers. The precision achieved through Machining Copper 101 ensures reliability and safety while reducing weight and increasing fuel efficiency for aircraft.
4. Telecommunications: Copper is an essential element in telecommunications infrastructure, cables, and connectors. Machining Copper 101 enables the production of high-performance parts with remarkable signal transmission capabilities, enhancing connectivity in the digital era.
IV. Conclusion:
As the demand for intricate components rises, manufacturers are turning to advanced machining solutions to ensure the highest levels of precision and durability. Machining Copper 101, developed by {Company Name}, unlocks the full potential of copper, revolutionizing the manufacturing landscape. With its unmatched precision, enhanced efficiency, extended durability, and cost-effectiveness, this groundbreaking technique promises a new era of precision manufacturing across industries. Embrace the power of Machining Copper 101 and stay ahead in the race for superior manufacturing excellence.
Company News & Blog
High-Quality Grinding Machine Parts: Essential Components for CNC Precision
Title: Revolutionizing the Grinding Industry: Innovative CNC Grinding Machine Parts Now AvailableIntroduction:In the ever-evolving world of manufacturing, precision and efficiency are key factors that decide the success of any company specializing in machining. While the demand for precision grinding machines continues to rise, businesses are constantly seeking innovative solutions to enhance their productivity and maintain a competitive edge. Recognizing this need, a leading manufacturer in the industry, [Company Name], is proud to announce the launch of their latest CNC grinding machine parts, designed to revolutionize the grinding process. These cutting-edge components promise to deliver unparalleled performance and accuracy, transforming the way manufacturers approach grinding operations.Unveiling the Latest CNC Grinding Machine Parts:[Company Name] has always been at the forefront of manufacturing advanced machinery components. Their new range of CNC grinding machine parts is no exception, pushing the boundaries of precision grinding to new heights. These state-of-the-art parts have been meticulously designed to cater to the needs of modern manufacturing processes, offering enhanced reliability and efficiency.Integrating advanced technologies and high-quality materials, [Company Name] has engineered their CNC grinding machine parts to optimize the grinding process, improving the overall production of manufacturers across various industries. From aerospace to automotive, medical to energy, these components ensure consistency, precision, and exceptional surface finishes.Key Advancements and Features:1. Enhanced Precision: The new CNC grinding machine parts boast advanced programming capabilities combined with high-speed controls, enabling manufacturers to achieve unprecedented precision in their grinding operations. This ensures superior quality outputs while minimizing the risk of errors and rework.2. Increased Efficiency: With cutting-edge automation features, the CNC grinding machine parts reduce manual intervention and increase operational efficiency. This not only streamlines the manufacturing process but also enables manufacturers to achieve higher production volumes in shorter turnaround times.3. Versatile Compatibility: These innovative components are designed to seamlessly integrate with various grinding machines, making them accessible and adaptable for a wide range of applications. Manufacturers can now leverage the benefits of this technology across multiple manufacturing setups without any significant overhaul or investment.4. Robust Durability: Engineered with longevity in mind, the CNC grinding machine parts from [Company Name] are built to withstand heavy loads and repeated usage. This ensures reliability and consistency even in the most demanding production environments, maximizing productivity and reducing downtime.Partnering with [Company Name]:Local and international manufacturers seeking to stay ahead in the machining industry can now benefit from the comprehensive range of CNC grinding machine parts provided by [Company Name]. Their exceptional dedication to research, development, and quality manufacturing sets them apart as a trusted partner in the industry.By relying on the expertise of [Company Name], manufacturers can enhance their production capabilities, significantly improve the quality of their products, and gain a competitive edge in the market. With their advanced CNC grinding machine parts, manufacturers will experience an immediate boost in productivity, efficiency, and customer satisfaction.Conclusion:As demand for precision components continues to rise in various industries, it is crucial for manufacturers to invest in cutting-edge technology that maximizes their capabilities. The introduction of the latest CNC grinding machine parts from [Company Name] revolutionizes the grinding process, offering manufacturers unmatched precision, efficiency, and durability. By integrating these advanced components into their machining setups, manufacturers can overcome challenges, streamline production, and deliver superior quality products to meet the dynamic demands of the market.
Top Advantages of High Precision Machining Centers for Superior Results
High-Precision Machining Center Revolutionizes Manufacturing Industry In today's competitive manufacturing landscape, precision and accuracy have become paramount for businesses looking to thrive. This need for precision has further intensified with growing demand for complex and intricate parts across various industries. To address this ever-increasing demand, a cutting-edge high-precision machining center has been developed, offering unparalleled accuracy and efficiency to revolutionize the manufacturing sector.The high-precision machining center, affectionately referred to as the HPMC, represents a groundbreaking advancement in machining technology. Designed to offer unmatched accuracy and versatility, this state-of-the-art solution ensures that even the most intricate parts are manufactured to precision, meeting the stringent quality requirements of modern industries. The HPMC's innovative and intelligent features provide manufacturers with the ability to tackle complex projects effortlessly, saving time and resources while achieving exceptional results.One of the key distinguishing features of this high-precision machining center is its advanced CNC control system. Leveraging cutting-edge technology, this control system allows for seamless programming and execution of machining operations with unparalleled precision. By providing operators with a user-friendly interface and an array of innovative features, this system ensures that the HPMC can handle a wide range of machining tasks efficiently and with utmost accuracy.Another standout characteristic of the HPMC is its robust construction and cutting-edge manufacturing techniques. Built with high-quality components, this machining center offers exceptional stability and rigidity, reducing vibrations and ensuring superior accuracy. Moreover, its innovative design minimizes heat generation during operation, which further contributes to its high-precision capabilities.In addition to its remarkable precision, the HPMC's versatility is yet another aspect that sets it apart from its competitors. With a multitude of available tooling options, the machining center can effortlessly handle a wide range of materials, from metals like steel and aluminum to composites and plastics. Its ability to accommodate various machining techniques, such as milling, drilling, and turning, makes it a highly versatile solution that can meet the diverse needs of manufacturers in different industries.Perhaps one of the most significant advantages of the HPMC is its potential to enhance productivity and efficiency. Equipped with innovative automation features and real-time monitoring capabilities, this machining center optimizes production processes and minimizes downtime. The intelligent workload management system ensures optimal operation, reducing idle time and maximizing productivity. Additionally, the HPMC's ability to integrate seamlessly with other Industry 4.0 technologies streamlines the entire manufacturing workflow, establishing a connected and efficient production environment.The importance of high-precision machining centers cannot be overstated. Their role in supporting the manufacturing industry is vital, as they enable businesses to meet the ever-increasing demands for accuracy, efficiency, and productivity. With the introduction of the HPMC, manufacturers can now stay ahead of the competition by delivering high-quality products with unmatched precision and efficiency.Leading the charge towards a new era of manufacturing excellence, the HPMC promises to transform the industry landscape. By combining state-of-the-art technology, unrivaled precision, and exceptional versatility, this machining center provides an all-encompassing solution for manufacturers striving for excellence. With the HPMC, businesses can confidently tackle complex projects, meet industry demands, and ensure their place at the forefront of the manufacturing industry.
Discover High-Quality Automotive Parts for CNC Applications
Title: Groundbreaking Innovations in Automobile Industry with Advanced CNC Automotive PartsIntroduction:With the ever-increasing demand for high-quality automotive components and a desire to revolutionize the automobile industry, a leading CNC automotive parts manufacturer has emerged as a game-changer in the market. Combining cutting-edge technology with superior craftsmanship, this company has redefined the standards of precision engineering and manufacturing. Providing a wide range of customized CNC automotive parts, they are paving the way for groundbreaking innovations in the automotive sector.Revolutionizing Manufacturing:In an industry where precision and reliability are paramount, this company has set a new benchmark for manufacturing excellence. Utilizing state-of-the-art CNC (Computer Numerical Control) machines, they have streamlined the production process, ensuring unrivaled accuracy and consistency. With their advanced machinery, the company can create intricate automotive parts that meet stringent quality standards. Each component undergoes rigorous testing and inspection to guarantee its durability and functionality.Expertise in Automotive Components:The company specializes in manufacturing a diverse range of CNC automotive parts. From engine components, such as cylinder heads and crankshafts, to transmission parts, like gear shafts and synchronizers, their portfolio covers all vital aspects of automobile functionality. Moreover, they also provide complex CNC parts for braking systems, suspension systems, and electrical components, ensuring a comprehensive solution for automotive manufacturers.Customization and Collaboration:One of the key strengths of this company is their ability to cater to the unique needs of their customers. They understand that each automotive manufacturer has specific requirements and work diligently to meet those demands. Whether it's a modification to an existing design or the creation of an entirely new component, they work closely with clients throughout the ideation, prototyping, and final production stages. By fostering collaborations, they ensure that automotive companies receive tailor-made CNC parts that perfectly integrate into their products.Commitment to Quality:Quality is at the heart of everything this company does. By adhering to strict quality control measures, they have earned a reputation for delivering flawless CNC automotive parts. Each phase of the manufacturing process is closely monitored, from material selection to the finishing touches. Additionally, the company's team of highly experienced engineers and technicians undergoes continuous training and improvement programs, ensuring they stay at the forefront of technological advancements and industry trends.Adapting to Changing Industry Demands:Recognizing the rapid evolution of the automobile industry, this company stays ahead of the curve when it comes to emerging trends and technologies. They invest in research and development, seeking innovative solutions to meet the changing demands of the automotive market. By embracing new materials, manufacturing techniques, and design principles, they offer cutting-edge CNC automotive parts that enhance overall vehicle performance, fuel efficiency, and safety.Global Reach and Customer Satisfaction:With a worldwide reach, the company exports its CNC automotive parts to numerous countries, ensuring automotive manufacturers worldwide have access to their exceptional products. Their commitment to customer satisfaction is evident in their prompt response times, competitive pricing, and on-time deliveries. By establishing long-term relationships with their clients, they ensure mutual success and contribute to the growth of the automobile industry.Conclusion:In an industry that demands precision, reliability, and innovation, this leading CNC automotive parts manufacturer has proven its mettle. With advanced manufacturing capabilities, customized solutions, and an unwavering commitment to quality, they are reshaping the automotive sector. By continuously pushing boundaries and embracing emerging technologies, they remain at the forefront of the industry, ushering in an era of groundbreaking innovations and advancements in automobile engineering.
Discover the Latest Developments in CNC Machining Turning Parts
Title: Innovations in CNC Machining Turning Parts Drive Efficiency and Precision in ManufacturingIntroduction:In the fast-paced world of manufacturing, CNC machining turning parts play a crucial role in creating high-quality products with optimal precision and efficiency. These parts are at the forefront of numerous industries, including aerospace, automotive, electronics, and more. One prominent company leading the charge in this field is {}, which has continuously pushed the boundaries of innovation in CNC machining turning parts to meet the ever-evolving needs of the industry.Body:I. Overview of CNC Machining Turning PartsCNC machining turning parts, also known as lathe parts, are essential components in modern manufacturing processes. These parts are created through computer numerical control (CNC) technology, ensuring precise and accurate shaping of various materials such as metals, plastics, and composites. They serve as the building blocks for intricate designs, enabling the creation of complex components with reduced lead time and improved efficiency.II. Advancements in CNC Machining Turning Parts by {}With a rich history and vast experience in the field, {} has emerged as a global leader in CNC machining turning parts. The company has consistently embraced cutting-edge technologies and innovative techniques to revolutionize the manufacturing landscape. Here are some key advancements pioneered by {}:a. High-speed machining: {} has developed high-speed CNC turning technology, significantly reducing production time without compromising quality. This innovation allows for faster material removal rates, higher spindle speeds, and enhanced surface finishes. By optimizing tool paths and utilizing advanced coolant systems, {} ensures that their CNC turning parts are manufactured with supreme precision.b. Multi-axis machining: To meet the demands of increasingly complex designs, {} has integrated multi-axis machining capabilities into their CNC turning processes. By utilizing advanced software and multi-axis turning centers, the company can produce intricate components with multiple geometries. This innovation eliminates the need for multiple setups, reducing production time and ensuring dimensional accuracy.c. Automation and robotics: Recognizing the importance of automation in modern manufacturing, {} has embraced robotics to enhance their CNC machining turning processes. The company has integrated robotic loading and unloading systems, reducing manual handling and increasing production efficiency. Automation also allows for continuous operation, reducing downtime and enhancing overall productivity.III. Industry Applications and BenefitsThe technological advancements achieved by {} in CNC machining turning parts have had a profound impact on various industry sectors. Some notable applications and associated benefits include:a. Aerospace: Precision and reliability are paramount in the aerospace industry. By using {}'s CNC turning parts, aerospace manufacturers can ensure the production of critical components with the highest degree of accuracy, contributing to enhanced safety and performance of aircraft.b. Automotive: In the automotive sector, where constant innovation and cost efficiency are key drivers, {}'s CNC turning parts enable the production of engine components, transmission parts, and precision gears. The high-speed machining capabilities provide unparalleled accuracy, allowing automakers to meet stringent performance standards.c. Electronics: With the growing demand for miniaturization and intricate designs in electronic devices, {}'s CNC turning parts cater to the production of connectors, contacts, and other sensitive components. Their multi-axis machining capabilities enable the fabrication of intricate structures, crucial for electronic devices' functionality.d. Medical: In the medical field, where precision and reliability are critical, {}'s CNC turning parts find extensive use in the manufacturing of surgical instruments, implants, and devices. The company's focus on high-speed machining ensures the quick production of high-quality medical components, contributing to improved patient outcomes.IV. Future Outlook and ConclusionAs technology continues to advance, the future of CNC machining turning parts looks promising. {} remains at the forefront of this industry, constantly pushing boundaries and exploring new horizons. The company's commitment to research and development, along with its dedication to delivering superior quality products, contributes to the thriving manufacturing sector. With {}'s innovative CNC machining turning parts, manufacturers across industries can unlock new levels of efficiency, precision, and competitiveness.In conclusion, CNC machining turning parts are the driving force behind the modern manufacturing industry's evolution. The advancements pioneered by {} have revolutionized the field, enabling the production of high-quality components with unmatched precision. By continuously exploring new frontiers in technology and embracing innovation, {}, devoid of brand name, continues to set new standards in CNC machining turning parts, proving itself as an industry leader in providing cutting-edge solutions to meet the evolving needs of manufacturing.
A Comprehensive Guide to Copper Machining Techniques
Title: Machining Copper 101: Unveiling the Next-Level Precision in ManufacturingIntroduction:In today's rapidly evolving industrial landscape, precision is of paramount importance. The demand for high-quality and intricate components has never been higher, prompting manufacturers to explore advanced machining techniques. In response to this growing need, {Company Name}, a renowned leader in the manufacturing industry, is unveiling its latest innovation - Machining Copper 101. This groundbreaking solution promises to revolutionize the way copper components are manufactured, providing unprecedented precision and durability. Let us delve deep into the world of Machining Copper 101 and its implications for various industries.I. Understanding Machining Copper 101:Machining Copper 101 is a cutting-edge manufacturing technique developed by {Company Name}, harnessing the full potential of copper as a versatile material. With its refined composition and exceptional conductive properties, copper has long been the go-to material for electrical connectors, printed circuit boards, and various precision parts. However, its notoriously challenging nature when it comes to machining has always posed a hurdle for manufacturers seeking complex and highly accurate components. Enter Machining Copper 101 - a game-changer that bridges the gap between precision and copper manufacturing.II. The Advantages of Machining Copper 101:1. Unmatched Precision: Machining Copper 101 leverages state-of-the-art technology, enabling manufacturers to achieve sub-micron level precision. This breakthrough ensures tighter tolerances and increased reliability, meeting the ever-increasing demands of diverse industries.2. Enhanced Efficiency: With Machining Copper 101, manufacturers can significantly reduce production time while maintaining impeccable quality. The optimized machining process eliminates the need for multiple operations, ultimately streamlining the manufacturing workflow.3. Extended Durability: By employing Machining Copper 101, components gain enhanced durability and longevity. The method optimizes the microstructure of the copper, resulting in improved resistance to wear, corrosion, and mechanical stress, making it suitable for demanding applications.4. Cost-effectiveness: The streamlined processes of Machining Copper 101 translate into reduced material waste, increased production throughput, and overall cost savings. Manufacturers can now provide superior products without compromising on profitability.III. Applications across Industries:The versatility of copper makes it a staple material across a wide range of industries. Machining Copper 101 opens up a plethora of options for manufacturers seeking to elevate their production standards in various sectors, including but not limited to:1. Electronics: Copper is indispensable in manufacturing electronic components like connectors, heat sinks, and advanced electrical systems. Machining Copper 101 allows for intricate designs and higher contact densities, bolstering the performance of electronic devices.2. Automotive: In the automotive sector, copper finds applications in wiring harnesses, sensors, brake systems, and engine components. With Machining Copper 101, manufacturers can create precise parts that ensure optimal functionality, efficiency, and safety.3. Aerospace: The aerospace industry relies heavily on copper for critical applications such as aircraft wiring, connectors, and heat exchangers. The precision achieved through Machining Copper 101 ensures reliability and safety while reducing weight and increasing fuel efficiency for aircraft.4. Telecommunications: Copper is an essential element in telecommunications infrastructure, cables, and connectors. Machining Copper 101 enables the production of high-performance parts with remarkable signal transmission capabilities, enhancing connectivity in the digital era.IV. Conclusion:As the demand for intricate components rises, manufacturers are turning to advanced machining solutions to ensure the highest levels of precision and durability. Machining Copper 101, developed by {Company Name}, unlocks the full potential of copper, revolutionizing the manufacturing landscape. With its unmatched precision, enhanced efficiency, extended durability, and cost-effectiveness, this groundbreaking technique promises a new era of precision manufacturing across industries. Embrace the power of Machining Copper 101 and stay ahead in the race for superior manufacturing excellence.
Premium Anodization Service: Exceptional Quality and Customization Offered
[Company Name] Introduces Anodization Service: Innovation Meets Durability[City, Date] - [Company Name], a leading provider of cutting-edge solutions, is pleased to announce the launch of its state-of-the-art anodization service. With a long-standing reputation for excellence in the industry, [Company Name] continues to push the boundaries of innovation by introducing this new offering.Anodization is a process that creates a protective oxide layer on the surface of metals, enhancing their durability, corrosion resistance, and aesthetics. [Company Name], known for its commitment to ensuring superior quality and customer satisfaction, aims to revolutionize the anodization process with its advanced technology and expertise.Through its anodization service, [Company Name] caters to a wide range of industries, including aerospace, automotive, electronics, and architecture. By leveraging their extensive experience and utilizing cutting-edge machinery, the company provides customers with an unmatched level of precision and customization.One of the key advantages of [Company Name]'s anodization service is the ability to offer a comprehensive range of colors and finishes. Whether clients require a sleek metallic appearance, vibrant colors, or a textured finish, [Company Name] can meet their exact specifications. This flexibility allows clients to enhance the visual appeal of their products while simultaneously providing them with increased durability.Furthermore, [Company Name]'s anodization process is environmentally friendly. By employing sustainable practices and utilizing eco-friendly materials, the company aims to minimize its carbon footprint and promote a greener future. This commitment to sustainability aligns with the broader industry shift towards eco-conscious manufacturing.The superior quality offered by [Company Name] is a result of their dedication to continuous improvement and adherence to stringent quality control measures. Each step of the anodization process is meticulously executed, ensuring that every product leaving [Company Name]'s facility meets the highest standards.To provide customers with added peace of mind, [Company Name] also offers a comprehensive warranty on its anodized products. This demonstrates the company's confidence in the durability and longevity of their solutions. Additionally, a highly skilled team of experts is always available to assist customers with any inquiries or technical support they may require.In celebration of the launch of their anodization service, [Company Name] is offering special incentives and discounts to new and existing clients for a limited time. This presents an excellent opportunity for businesses to experience the benefits of anodization while taking advantage of unprecedented cost savings.By introducing its anodization service, [Company Name] cements its position as an industry leader, continuously pushing the boundaries of innovation. The company's commitment to quality, sustainability, and customer satisfaction ensures that their anodized products will have a lasting impact on various industries.About [Company Name]:Established in [Year], [Company Name] has been a frontrunner in delivering cutting-edge solutions to a diverse range of industries. With a highly skilled team and state-of-the-art technology, the company continues to provide superior quality and customer service. By combining innovation, durability, and a commitment to sustainability, [Company Name] sets itself apart from its competitors.For more information about [Company Name]'s anodization service and to explore their comprehensive range of solutions, please visit their website [Website URL] or contact their customer service team at [Phone Number].
Mastering the Art of Machining High-Strength 7075 Aluminum
Machining 7075 Aluminum Revolutionizes Manufacturing ProcessesIn today's rapidly evolving world, manufacturing companies are constantly on the lookout for innovative solutions to optimize their manufacturing processes and deliver high-quality products. This quest for excellence has led many companies to explore and adopt advanced materials that offer exceptional performance and durability. One such material is the remarkable 7075 aluminum, a game-changer in the manufacturing industry.Renowned for its exceptional strength-to-weight ratio, 7075 aluminum has become the go-to material for aerospace, automotive, marine, and defense industries. This high-strength aluminum alloy possesses excellent mechanical properties, making it perfect for applications that require superior strength, minimal weight, and exceptional resistance to corrosion. With an ultimate tensile strength of over 570 MPa (83000 psi) unmatched by other aluminum alloys, it has cemented its place as a preferred material for various critical components.However, working with 7075 aluminum has traditionally been a significant challenge due to its hardness. The machinability of any material plays a vital role in determining the manufacturing process's efficiency and productivity. This is where cutting-edge technologies, combined with expertise and innovation, have revolutionized the machining of 7075 aluminum, enabling manufacturing companies to unlock its full potential.Leading the charge in this machining revolution is a renowned company specializing in advanced manufacturing techniques, which prefers to remain anonymous. By adopting state-of-the-art machinery, cutting tools, and software solutions, they have successfully overcome the hurdles associated with machining 7075 aluminum, blazing a trail for others to follow.At the heart of this remarkable accomplishment lies a deep understanding of the material and its unique properties. The company has invested in cutting-edge CNC machining centers and high-speed machining technology that can handle the challenging requirements of 7075 aluminum. These advanced machines offer enhanced rigidity, stability, and precision, enabling manufacturers to achieve intricate designs, tight tolerances, and superior surface finishes.To ensure maximum efficiency during the machining process, novel tooling systems have been developed to optimize the removal of material. With carefully designed tool geometries, coatings, and cutting parameters, the company has created tooling solutions that significantly reduce machining time and increase tool life. This results in higher productivity, lower costs, and the ability to handle large-scale production needs.Furthermore, the company has embraced the power of Computer-Aided Manufacturing (CAM) software, enabling them to efficiently program and simulate machining operations. This software allows manufacturers to predict and optimize tool paths, simulate machining processes, and eliminate potential errors or collisions. By leveraging CAM software, manufacturers can fine-tune their machining strategies, reduce setup times, and ensure utmost accuracy, resulting in consistent and precise manufacturing of 7075 aluminum components.The company's expertise in machining 7075 aluminum has also sparked innovation in surface finishing techniques. By leveraging advanced polishing and deburring processes, they have perfected the art of producing components with exceptional surface quality. This attention to detail ensures that the manufactured parts not only possess high strength but also exhibit an aesthetically pleasing appearance.As manufacturers across various industries recognize the advantages of utilizing 7075 aluminum, the pioneering work of this anonymous company is set to have a significant impact on the manufacturing landscape. With their expertise, commitment to innovation, and state-of-the-art machinery, they have set a new standard for machining 7075 aluminum, enabling manufacturers worldwide to leverage its outstanding properties efficiently.In conclusion, the machining of 7075 aluminum has undergone a monumental transformation in recent years, thanks to the efforts of cutting-edge manufacturing companies. With their expertise, innovative technologies, and dedication to perfection, these companies have overcome traditional challenges associated with working with this exceptional material. Consequently, the manufacturing industry can now fully exploit the remarkable properties of 7075 aluminum, revolutionizing the production of critical components across various sectors.
Mastering the Art of Machining 4140 Steel – Your Ultimate Guide
Machining of 4140 Steel: The Perfect Blend of Durability and PrecisionIn the realm of fabrication and manufacturing, the importance of finding the right materials cannot be overstated. From aerospace engineering to automotive applications, industries across the board rely on high-quality materials that possess exceptional strength, durability, and precision. One such material that meets these criteria with flying colors is 4140 steel, which has become increasingly popular due to its remarkable mechanical properties and versatility. In this article, we delve into the world of machining 4140 steel and explore how it has revolutionized the field of fabrication.Before we delve into the specifics of machining 4140 steel, it is essential to understand its unique composition and properties. 4140 steel is a low-alloy steel that contains chromium, molybdenum, and manganese, which contribute to its exceptional strength and toughness. It has a high hardenability, making it suitable for applications requiring a robust and durable material that can withstand significant stress and pressure. Additionally, 4140 steel offers excellent wear resistance, making it ideal for high-temperature and abrasive environments.With its impressive characteristics, 4140 steel has found widespread use in various industries, including aerospace, automotive, oil and gas, and defense. It is employed in the manufacturing of critical components such as gears, shafts, axles, and spindles, where its strength and durability are highly valued. Moreover, machining 4140 steel has become an essential process in the fabrication of these components, ensuring utmost precision and quality.When it comes to machining 4140 steel, the industry leader, {}, stands at the forefront. With years of experience and a stellar reputation, {} has perfected the art of machining this remarkable material. They employ state-of-the-art technologies and cutting-edge machinery, allowing for exceptional accuracy, efficiency, and consistency.The process of machining 4140 steel begins with careful planning and a thorough understanding of the component's specifications. {} collaborates closely with their clients, ensuring clear communication and a comprehensive comprehension of the desired outcome. Once the parameters are established, their team of skilled engineers and technicians employs a range of precise machining techniques, including milling, turning, drilling, and grinding, to transform raw 4140 steel into highly intricate and accurately shaped components.One of the primary challenges in machining 4140 steel lies in its high hardness. However, {} has developed innovative machining strategies and cutting tool technologies that overcome these hurdles with ease. Through the utilization of cooled cutting tools, advanced lubricants, and optimized cutting parameters, they ensure extended tool life, reduced machining time, and impeccable surface finishes. Their commitment to research and development enables them to stay ahead of the curve, continuously evolving their machining processes to deliver unparalleled results.In addition to their technical prowess, {} places immense emphasis on quality control throughout the entire machining process. Rigorous inspection procedures and strict adherence to industry standards guarantee that each component meets the most stringent requirements. This dedication to quality has earned them accolades from clients across diverse sectors, solidifying their position as a trusted partner in the realm of fabrication.As the demand for superior components continues to grow, machining 4140 steel remains an essential process for companies aspiring to deliver excellence. With their unrivaled expertise and unwavering commitment to precision, {} emerges as the ultimate choice for machining this exceptional material. By harnessing the remarkable characteristics of 4140 steel and combining it with their cutting-edge technologies, {} ensures the creation of components that redefine the boundaries of strength, durability, and accuracy.In conclusion, machining 4140 steel has revolutionized the field of fabrication, offering unparalleled strength, durability, and precision. Whether it's the aerospace industry, automotive applications, or defense mechanisms, the versatility of this material makes it the go-to choice for manufacturers worldwide. With {} leading the way in machining 4140 steel, the future of fabrication looks promising as it continues to push the boundaries of what is possible in terms of component quality and performance.
Get Superior Custom Cut Gears for Precision Mechanical Applications
Custom Cut Gears Launches New Line of High-Quality Gears for Industrial Applications[City, State] – [Date] – Custom Cut Gears, a leading manufacturer of precision gears, announced today the launch of their latest line of high-quality gears designed for industrial applications. With their commitment to excellence and state-of-the-art manufacturing processes, Custom Cut Gears aims to provide top-notch solutions to meet the specific needs of various industries.With over 20 years of experience in the industry, Custom Cut Gears has built a reputation for delivering gears of the highest quality that meet or exceed customer requirements. Their team of skilled engineers and technicians specialize in producing gears with exceptional precision, durability, and performance. This new line of gears further solidifies their position as an industry leader.The newly launched line of gears caters to a wide range of industrial applications, including automotive, aerospace, robotics, marine, and more. Custom Cut Gears offers a diverse selection of gear types, such as spur gears, helical gears, bevel gears, worm gears, and planetary gears, among others. This extensive range ensures that customers can find the perfect gear solution for their specific application.What sets Custom Cut Gears apart is their commitment to customization. They understand that each industry has unique requirements, and thus offer customization options to tailor gears to the precise needs of their customers. From material selection to tooth profile modifications, customers can work with Custom Cut Gears to optimize the gears' performance for their specific applications. This level of flexibility ensures that customers receive gears that not only meet their requirements but also enhance their overall efficiency and productivity.Furthermore, all gears manufactured by Custom Cut Gears undergo rigorous quality control processes to ensure the highest level of accuracy and reliability. Their state-of-the-art facility is equipped with advanced machinery and inspection systems, enabling them to maintain tight tolerances and consistent quality across every gear produced. Custom Cut Gears adheres to strict industry standards and certifications, demonstrating their commitment to delivering products of the utmost integrity."We are thrilled to introduce our new line of high-quality gears for industrial applications," said [Spokesperson's Name], spokesperson for Custom Cut Gears. "Our team has put in tremendous effort to develop gears that not only meet industry standards but also exceed customer expectations. With our focus on customization, we aim to provide gears that empower our customers to achieve optimal performance in their respective applications."Custom Cut Gears has collaborated with numerous customers across various industries and successfully helped them solve complex gear-related challenges. Their team of experts works closely with clients to understand their unique requirements and develop gear solutions that deliver exceptional results. The combination of expertise, customization options, and dedication to quality makes them the preferred choice for many companies worldwide.As Custom Cut Gears continues to grow, they remain committed to investing in research and development to stay ahead of industry trends. They are constantly exploring new technologies and techniques to improve their manufacturing processes and design capabilities. This commitment ensures that their customers receive innovative and reliable gear solutions that align with the rapidly evolving industrial landscape.About Custom Cut Gears: Custom Cut Gears is a leading manufacturer of precision gears, specializing in the production of high-quality gears for various industrial applications. With over 20 years of experience, their skilled team of engineers and technicians deliver customized gear solutions that meet the specific needs of their diverse clientele. Custom Cut Gears' commitment to excellence, customization, and quality sets them apart as a trusted gear manufacturer in the industry.For more information about Custom Cut Gears and their range of products, please visit [website] or contact [contact information].
Discover the Top CNC Machining Companies for Quality Precision Manufacturing
Title: Cnc Machining Companies Revolutionize Precision ManufacturingSubtitle: Embracing Cutting-Edge Technology and Unrivaled ExpertiseDate: [Insert Date][City, State] - In an era where precision and efficiency dominate the manufacturing industry, Cnc Machining Companies are pioneering the way forward. By harnessing advanced technologies and their unparalleled expertise, these companies are revolutionizing the world of manufacturing.Cnc Machining Companies are renowned for their ability to provide high-quality, precise, and versatile manufactured parts across various industries. Their commitment to excellence and a client-centric approach has solidified their reputation as market leaders in the machining industry.Founded on the principles of innovation and delivering beyond customer expectations, [Company Name] has emerged as one of the frontrunners among Cnc Machining Companies. With their cutting-edge facilities and team of seasoned professionals, they have successfully carved a niche for themselves in the market.By constantly investing in state-of-the-art equipment, [Company Name] ensures that they are at the forefront of technological advancements within the industry. This allows them to offer a vast array of machining services, ranging from milling, turning, drilling, to grinding, along with a host of other specialized techniques.The company places great importance on their team, which consists of highly skilled engineers, machinists, and technicians who collectively possess an extensive pool of knowledge and expertise. Moreover, [Company Name] promotes a culture of continuous improvement, ensuring that their workforce receives regular training to stay updated with the latest trends and techniques in the industry.By leveraging their technological prowess and skilled workforce, [Company Name] caters to a diverse client base spanning various industries such as aerospace, automotive, electronics, medical equipment, and many more. They understand that each industry has its unique requirements, and they strive to provide tailored solutions that meet and exceed customer expectations.From conceptualization to execution, [Company Name] provides end-to-end support to their clients. They work closely with their customers to understand their specific needs, allowing the company to produce exceptionally precise parts that align perfectly with their requirements. Whether it be prototyping or the mass production of intricate components, [Company Name] has the capabilities to deliver on time and with impeccable precision.Quality control is a cornerstone of [Company Name]'s operations. Equipped with stringent quality assurance measures and advanced inspection equipment, they ensure that every manufactured component undergoes rigorous testing. This commitment to precision and quality has earned [Company Name] numerous certifications, further solidifying their reputation as a trusted partner in the industry.In addition to their focus on delivering exceptional quality, [Company Name] is also committed to minimizing their environmental impact. They continuously strive to improve their manufacturing processes to optimize energy consumption and reduce waste generation. By embracing sustainable practices, [Company Name] aims to contribute to a greener and more sustainable future.Cnc Machining Companies like [Company Name] are not just manufacturers; they are partners in progress for their clients. Their ability to provide high-quality parts with unmatched precision has helped industries redefine what is possible. By embracing cutting-edge technology, an unwavering commitment to excellence, and an unrelenting focus on customer satisfaction, these companies are shaping the future of the manufacturing industry.About [Company Name]:[Company Name] is an industry-leading CNC machining company specializing in providing high-quality, precise, and versatile manufacturing solutions. With state-of-the-art facilities and a dedicated team of experts, they offer a wide range of machining services for diverse industries. Committed to excellence and customer satisfaction, [Company Name] prides itself on delivering exceptional quality and personalized solutions.For further inquiries or more information, please visit [Company Website] or contact [Company Contact].Press Contact:[Company Name][Contact Person][Title][Email][Phone]