Mastering the Process of 5 Axis Milling in Manufacturing
By:Admin
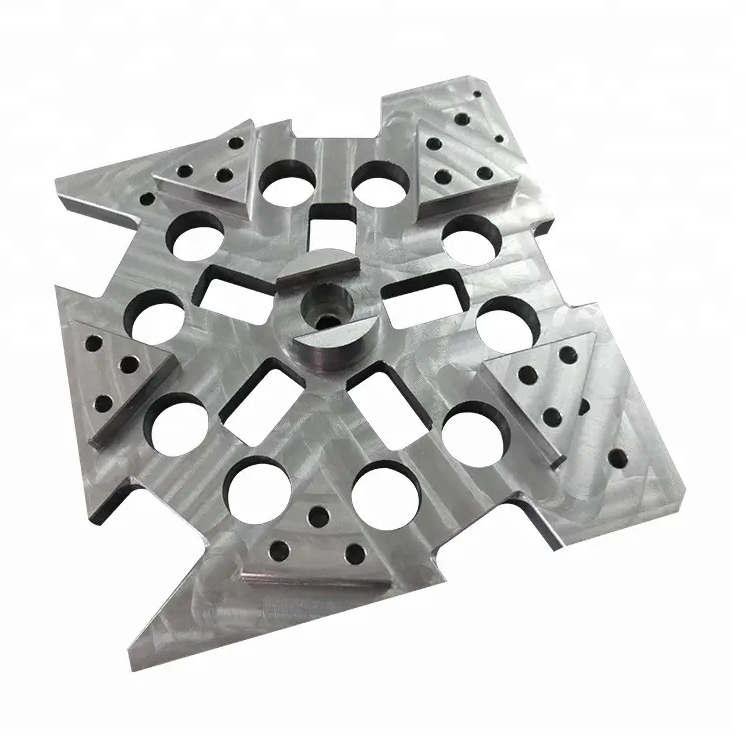
{}, a leading manufacturer in the industry, has recently implemented cutting-edge 5 Axis Milling technology into their production process, revolutionizing the way they manufacture their products. This new technology has allowed them to significantly improve their productivity, accuracy, and efficiency, positioning them at the forefront of innovation in the manufacturing sector.
5 Axis Milling is a advanced manufacturing process that enables the production of highly complex parts and components with unmatched precision. Unlike traditional 3 axis or 4 axis milling, 5 axis milling allows for greater flexibility and efficiency in machining operations, as it enables the cutting tool to move across five different axes simultaneously. This multi-directional movement capability enables the production of intricately shaped parts and components, with minimal setup and machining time.
At {}, the integration of 5 Axis Milling technology has resulted in a substantial increase in productivity and a dramatic improvement in the quality of their products. With the ability to perform complex machining operations in a single setup, the company has been able to reduce the number of required machining operations, minimize the need for manual intervention, and significantly decrease lead times. This has not only allowed them to expedite their production process, but also to meet the growing demand for their high-quality products more efficiently.
Moreover, the enhanced precision and accuracy achieved through 5 Axis Milling has enabled {} to consistently manufacture parts and components with incredibly tight tolerances. This level of precision has not only improved the overall quality of their products, but has also minimized the need for secondary operations and post-machining adjustments. As a result, the company has been able to reduce waste, improve cost-efficiency, and maintain a competitive edge in the market.
In addition to the operational benefits, the implementation of 5 Axis Milling has also allowed {} to expand their capabilities and take on more complex and challenging projects. The technology has empowered their engineering team to push the boundaries of design and innovation, as they now have the ability to manufacture highly intricate and geometrically complex parts that were previously unattainable with traditional machining processes. This has opened up new opportunities for the company to diversify their product offerings and cater to a wider range of industries and applications.
Furthermore, the investment in 5 Axis Milling technology reflects {}'s commitment to staying at the forefront of technological advancement in the manufacturing sector. By continuously integrating the latest and most advanced machinery and processes, the company demonstrates its dedication to delivering the highest quality products and services to its customers. This forward-thinking approach not only positions them as a leader in the industry, but also ensures their long-term sustainability and growth in an increasingly competitive market.
With the successful implementation of 5 Axis Milling technology, {} has raised the bar for manufacturing excellence, setting a new standard for precision, efficiency, and innovation in the industry. As they continue to harness the power of this advanced technology, the company is poised to further strengthen its position as a preferred partner for high-quality, custom-manufactured parts and components across various sectors. Their relentless pursuit of excellence and their willingness to embrace new technology undoubtedly sets them apart as a trailblazer in the manufacturing landscape.
Company News & Blog
CNC Lathe Machine Parts: Essential Components for Efficient Precision Machining
Title: Revolutionizing Precision Manufacturing with Advanced CNC Lathe Machine PartsIntroduction:In today's rapidly evolving manufacturing industry, technological advancements play a crucial role in enhancing efficiency and precision. One such revolutionizing development is the integration of innovative CNC lathe machine parts. With their state-of-the-art attributes and cutting-edge functionality, these components are revolutionizing precision manufacturing processes across various sectors.Company Overview:As a leading provider of CNC lathe machine parts, our company has established itself as an industry pioneer, continuously pushing the boundaries of innovation. We strive to deliver exceptional precision engineering solutions that cater to the diverse needs of our esteemed clientele. With a commitment to quality, reliability, and staying ahead of the curve, our products have garnered immense recognition and trust in the market.Body:1. Introduction to CNC Lathe Machine Parts:CNC (Computer Numerical Control) lathe machine parts have transformed traditional machining practices by offering unparalleled precision, efficiency, and flexibility. These parts are designed to fit into computer-controlled lathes, which enables automated and highly accurate machining operations. By utilizing advanced software and cutting-edge technology, CNC lathe machine parts have become indispensable tools in industries such as automotive, aerospace, electronics, and medical equipment manufacturing.2. Key Features and Benefits:a) Enhanced Precision: CNC lathe machine parts are equipped with advanced sensors and control systems, which ensure unprecedented accuracy, consistency, and repeatability. This level of precision results in superior product quality and reduced waste, making them ideal for intricate and critical components.b) Simplified Operations: With integrated computerized controls, CNC lathe machine parts provide user-friendly interfaces that require minimal manual intervention. The ability to automate complex machining processes significantly reduces human error, labor costs, and production time.c) Versatility and Flexibility: These components offer extensive customization options, allowing manufacturers to adapt their machining operations to a diverse range of materials, geometries, and specifications. This flexibility enables companies to fulfill customer demands efficiently, even for small production runs.d) Increased Efficiency: Through efficient cutting strategies and optimized tool paths, CNC lathe machine parts significantly improve productivity by reducing cycle times and maximizing machine utilization. This increased efficiency enables manufacturers to meet demanding deadlines and scale production seamlessly.e) Cost-Effectiveness: Although CNC lathe machine parts have a higher initial investment, their long-term cost-effectiveness cannot be overlooked. Their precision and efficiency lead to substantial material and time savings, reducing overall production costs and boosting profitability in the long run.3. Range of CNC Lathe Machine Parts:Our company offers an extensive range of CNC lathe machine parts that cater to various industry requirements. These parts include but are not limited to:a) Spindles and Chuck Systems: These critical components are responsible for holding and rotating the workpiece during machining operations. Our advanced spindles and chuck systems ensure stable and accurate positioning, contributing to the overall precision and quality of the finished products.b) Tool Holders and Accessories: Our tool holders are designed to securely hold cutting tools and optimize their performance. With excellent vibration dampening properties and quick-change systems, these accessories enhance machining stability and reduce tool changeover times.c) Control Systems and Software: We provide cutting-edge control systems and software that integrate seamlessly with CNC lathe machines. These systems offer an intuitive user interface, intelligent tool management, and advanced programming capabilities, enabling manufacturers to achieve precise and efficient machining.d) Cutting Tools: Our comprehensive range of cutting tools includes inserts, drills, and milling cutters designed for various materials and machining requirements. These high-performance tools ensure exceptional machining accuracy and prolong tool life, further optimizing production processes.4. Customer Success Stories: Highlighting success stories of our customers who have benefited from incorporating CNC lathe machine parts in their operations will depict the significant impact these components have had on their businesses. Case studies demonstrating increased productivity, improved quality, and higher cost-efficiency will add credibility to the news content.Conclusion:The integration of advanced CNC lathe machine parts has marked a significant paradigm shift in precision manufacturing. With their unrivaled precision, user-friendly interfaces, and versatility, these components are empowering manufacturers across industries to enhance their competitiveness and achieve outstanding results. As a leading provider of CNC lathe machine parts, our company continues to drive innovation and deliver exceptional solutions that redefine precision machining standards.
A Comprehensive Guide to Copper Machining Techniques
Title: Machining Copper 101: Unveiling the Next-Level Precision in ManufacturingIntroduction:In today's rapidly evolving industrial landscape, precision is of paramount importance. The demand for high-quality and intricate components has never been higher, prompting manufacturers to explore advanced machining techniques. In response to this growing need, {Company Name}, a renowned leader in the manufacturing industry, is unveiling its latest innovation - Machining Copper 101. This groundbreaking solution promises to revolutionize the way copper components are manufactured, providing unprecedented precision and durability. Let us delve deep into the world of Machining Copper 101 and its implications for various industries.I. Understanding Machining Copper 101:Machining Copper 101 is a cutting-edge manufacturing technique developed by {Company Name}, harnessing the full potential of copper as a versatile material. With its refined composition and exceptional conductive properties, copper has long been the go-to material for electrical connectors, printed circuit boards, and various precision parts. However, its notoriously challenging nature when it comes to machining has always posed a hurdle for manufacturers seeking complex and highly accurate components. Enter Machining Copper 101 - a game-changer that bridges the gap between precision and copper manufacturing.II. The Advantages of Machining Copper 101:1. Unmatched Precision: Machining Copper 101 leverages state-of-the-art technology, enabling manufacturers to achieve sub-micron level precision. This breakthrough ensures tighter tolerances and increased reliability, meeting the ever-increasing demands of diverse industries.2. Enhanced Efficiency: With Machining Copper 101, manufacturers can significantly reduce production time while maintaining impeccable quality. The optimized machining process eliminates the need for multiple operations, ultimately streamlining the manufacturing workflow.3. Extended Durability: By employing Machining Copper 101, components gain enhanced durability and longevity. The method optimizes the microstructure of the copper, resulting in improved resistance to wear, corrosion, and mechanical stress, making it suitable for demanding applications.4. Cost-effectiveness: The streamlined processes of Machining Copper 101 translate into reduced material waste, increased production throughput, and overall cost savings. Manufacturers can now provide superior products without compromising on profitability.III. Applications across Industries:The versatility of copper makes it a staple material across a wide range of industries. Machining Copper 101 opens up a plethora of options for manufacturers seeking to elevate their production standards in various sectors, including but not limited to:1. Electronics: Copper is indispensable in manufacturing electronic components like connectors, heat sinks, and advanced electrical systems. Machining Copper 101 allows for intricate designs and higher contact densities, bolstering the performance of electronic devices.2. Automotive: In the automotive sector, copper finds applications in wiring harnesses, sensors, brake systems, and engine components. With Machining Copper 101, manufacturers can create precise parts that ensure optimal functionality, efficiency, and safety.3. Aerospace: The aerospace industry relies heavily on copper for critical applications such as aircraft wiring, connectors, and heat exchangers. The precision achieved through Machining Copper 101 ensures reliability and safety while reducing weight and increasing fuel efficiency for aircraft.4. Telecommunications: Copper is an essential element in telecommunications infrastructure, cables, and connectors. Machining Copper 101 enables the production of high-performance parts with remarkable signal transmission capabilities, enhancing connectivity in the digital era.IV. Conclusion:As the demand for intricate components rises, manufacturers are turning to advanced machining solutions to ensure the highest levels of precision and durability. Machining Copper 101, developed by {Company Name}, unlocks the full potential of copper, revolutionizing the manufacturing landscape. With its unmatched precision, enhanced efficiency, extended durability, and cost-effectiveness, this groundbreaking technique promises a new era of precision manufacturing across industries. Embrace the power of Machining Copper 101 and stay ahead in the race for superior manufacturing excellence.
Discover the Latest Developments in CNC Machining Turning Parts
Title: Innovations in CNC Machining Turning Parts Drive Efficiency and Precision in ManufacturingIntroduction:In the fast-paced world of manufacturing, CNC machining turning parts play a crucial role in creating high-quality products with optimal precision and efficiency. These parts are at the forefront of numerous industries, including aerospace, automotive, electronics, and more. One prominent company leading the charge in this field is {}, which has continuously pushed the boundaries of innovation in CNC machining turning parts to meet the ever-evolving needs of the industry.Body:I. Overview of CNC Machining Turning PartsCNC machining turning parts, also known as lathe parts, are essential components in modern manufacturing processes. These parts are created through computer numerical control (CNC) technology, ensuring precise and accurate shaping of various materials such as metals, plastics, and composites. They serve as the building blocks for intricate designs, enabling the creation of complex components with reduced lead time and improved efficiency.II. Advancements in CNC Machining Turning Parts by {}With a rich history and vast experience in the field, {} has emerged as a global leader in CNC machining turning parts. The company has consistently embraced cutting-edge technologies and innovative techniques to revolutionize the manufacturing landscape. Here are some key advancements pioneered by {}:a. High-speed machining: {} has developed high-speed CNC turning technology, significantly reducing production time without compromising quality. This innovation allows for faster material removal rates, higher spindle speeds, and enhanced surface finishes. By optimizing tool paths and utilizing advanced coolant systems, {} ensures that their CNC turning parts are manufactured with supreme precision.b. Multi-axis machining: To meet the demands of increasingly complex designs, {} has integrated multi-axis machining capabilities into their CNC turning processes. By utilizing advanced software and multi-axis turning centers, the company can produce intricate components with multiple geometries. This innovation eliminates the need for multiple setups, reducing production time and ensuring dimensional accuracy.c. Automation and robotics: Recognizing the importance of automation in modern manufacturing, {} has embraced robotics to enhance their CNC machining turning processes. The company has integrated robotic loading and unloading systems, reducing manual handling and increasing production efficiency. Automation also allows for continuous operation, reducing downtime and enhancing overall productivity.III. Industry Applications and BenefitsThe technological advancements achieved by {} in CNC machining turning parts have had a profound impact on various industry sectors. Some notable applications and associated benefits include:a. Aerospace: Precision and reliability are paramount in the aerospace industry. By using {}'s CNC turning parts, aerospace manufacturers can ensure the production of critical components with the highest degree of accuracy, contributing to enhanced safety and performance of aircraft.b. Automotive: In the automotive sector, where constant innovation and cost efficiency are key drivers, {}'s CNC turning parts enable the production of engine components, transmission parts, and precision gears. The high-speed machining capabilities provide unparalleled accuracy, allowing automakers to meet stringent performance standards.c. Electronics: With the growing demand for miniaturization and intricate designs in electronic devices, {}'s CNC turning parts cater to the production of connectors, contacts, and other sensitive components. Their multi-axis machining capabilities enable the fabrication of intricate structures, crucial for electronic devices' functionality.d. Medical: In the medical field, where precision and reliability are critical, {}'s CNC turning parts find extensive use in the manufacturing of surgical instruments, implants, and devices. The company's focus on high-speed machining ensures the quick production of high-quality medical components, contributing to improved patient outcomes.IV. Future Outlook and ConclusionAs technology continues to advance, the future of CNC machining turning parts looks promising. {} remains at the forefront of this industry, constantly pushing boundaries and exploring new horizons. The company's commitment to research and development, along with its dedication to delivering superior quality products, contributes to the thriving manufacturing sector. With {}'s innovative CNC machining turning parts, manufacturers across industries can unlock new levels of efficiency, precision, and competitiveness.In conclusion, CNC machining turning parts are the driving force behind the modern manufacturing industry's evolution. The advancements pioneered by {} have revolutionized the field, enabling the production of high-quality components with unmatched precision. By continuously exploring new frontiers in technology and embracing innovation, {}, devoid of brand name, continues to set new standards in CNC machining turning parts, proving itself as an industry leader in providing cutting-edge solutions to meet the evolving needs of manufacturing.
CNC Parts Manufacturer Offers High-Quality Components for Various Industries
Title: Leading CNC Parts Manufacturer Sets New Industry Standards for Precision and Quality Introduction:In today's technologically advanced era, CNC parts play a crucial role in manufacturing industries worldwide. They are instrumental in creating precision components that form the foundation of various products and equipment. A renowned CNC parts manufacturer, we strive to meet and exceed industry standards by delivering exceptional quality, precision, and reliability in every component we produce. With the latest machinery, cutting-edge technology, and a team of highly skilled professionals, we consistently deliver superior CNC parts to industries across the globe.Indisputable Leadership in Manufacturing Excellence:Our company's unwavering commitment to precision, quality, and innovation has firmly established us as a leader in the CNC parts manufacturing sector. For over a decade, we have been at the forefront of setting new industry standards for excellence. Our dedication to providing unmatched quality has earned us the trust and loyalty of diverse industries such as aerospace, automotive, electronics, and healthcare.Cutting-Edge Machinery and Technology:Our production process is empowered by state-of-the-art machinery and cutting-edge technology. This synergy allows us to manufacture CNC parts with unrivaled precision, accuracy, and repeatability. We continually invest in cutting-edge machinery to ensure that our capabilities remain at the forefront of the industry. Our advanced machinery also enables us to meet complex design specifications and deliver customized solutions tailored to our clients' unique needs.Highly Skilled Workforce:Behind our success lies a team of highly skilled professionals who possess unparalleled expertise in the field of CNC part manufacturing. Our engineers, technicians, and quality control personnel are committed to excellence in every aspect of our operations. They undergo regular training to stay updated with the latest manufacturing techniques, ensuring our parts adhere to the highest quality standards. Our workforce's vast knowledge, coupled with their tireless dedication, enables us to consistently deliver precision-engineered components.Stringent Quality Assurance:Quality is the cornerstone of our company's philosophy. Our commitment to providing superior CNC parts is unparalleled, and we leave no stone unturned in adhering to stringent quality control measures. From raw material selection to the final product inspection, our quality control teams meticulously monitor and inspect every step of the manufacturing process. This rigorous approach guarantees that our clients receive only the highest quality CNC parts, backed by comprehensive documentation and certifications.Client-Centric Approach:At our company, we believe in building long-term relationships with our clients. We understand that every client has unique requirements, and we pride ourselves on offering personalized solutions to meet their specific needs. We collaborate closely with our clients, from the initial design phase to the final product delivery, ensuring transparent communication and efficient project management. Our commitment to client satisfaction drives us to consistently exceed their expectations and solidify our reputation as a trusted partner.Global Reach and Commitment to Sustainability:Our dedication to excellence knows no boundaries. With a global reach, we have supplied CNC parts to customers in various countries, establishing ourselves as a reliable international partner. Simultaneously, we are committed to sustainable manufacturing practices. By reducing energy consumption, optimizing raw material usage, and implementing eco-friendly processes, we strive to reduce our environmental footprint and contribute positively to a greener future.Conclusion:As a leading CNC parts manufacturer, we set new industry standards by delivering superior precision, quality, and reliability in every component we produce. Our cutting-edge machinery, advanced technology, highly skilled workforce, and commitment to stringent quality control make us a trusted partner for industries globally. With a client-centric approach and commitment to sustainability, we are ready to shape the future of precision engineering, one CNC part at a time.
Comparison: Machining 304 Stainless Steel vs 316 Stainless Steel
Title: A Comparative Analysis: Machining 304 Vs 316 Stainless SteelIntroduction:In the world of metal fabrication and manufacturing, stainless steel is one of the most widely used materials due to its exceptional corrosion resistance and durability. Two common stainless steel varieties are 304 and 316, both known for their unique properties and applications across various industries. In this article, we will delve into a comparative analysis of machining these stainless steel grades, exploring their characteristics, benefits, and potential applications.Machining 304 Stainless Steel:304 stainless steel, a versatile and widely-used material, offers excellent corrosion resistance, high-temperature resistance, and good formability. It is commonly found in food processing equipment, kitchen appliances, and architectural applications. Machining 304 stainless steel presents several advantages, making it a preferred choice in many manufacturing processes.1. Machinability: 304 stainless steel offers excellent machinability due to its lower carbon content compared to other stainless steel grades. This characteristic promotes efficient chip formation, resulting in improved tool life and reduced cycle times for machining processes.2. Cuttability: The relatively lower hardness of 304 stainless steel makes it easier to cut, reducing machine wear and tear. It can be quickly drilled, tapped, milled, and turned, enabling manufacturers to achieve precise and intricate designs effortlessly.3. Weldability: 304 stainless steel exhibits superior weldability, allowing for easy and efficient joining with a variety of techniques, including TIG and MIG welding. This facilitates the fabrication of complex structures and components without compromising the material's strength and integrity.4. Surface Finish: Machined 304 stainless steel can achieve a smooth and lustrous surface finish, making it ideal for applications where aesthetics play a crucial role, such as architectural elements or decorative pieces.Machining 316 Stainless Steel:316 stainless steel, often referred to as marine-grade stainless steel, is known for its outstanding resistance to corrosive environments, particularly chloride-containing solutions. Due to its superior corrosion resistance, it finds applications in marine equipment, chemical processing plants, and medical devices. While machining 316 stainless steel presents some challenges, it offers unique benefits that make it indispensable in specific industries.1. Hardness: Compared to 304 stainless steel, 316 stainless steel has a slightly higher hardness. While this makes machining more demanding, it also contributes to its enhanced strength, ideal for heavy-duty applications where mechanical strength is paramount.2. Heat Resistance: 316 stainless steel exhibits excellent high-temperature resistance, making it suitable for applications involving extreme heat, such as heat exchangers and furnace parts. The material's ability to withstand prolonged exposure to elevated temperatures adds to its versatility in various industrial settings.3. Corrosion Resistance: The corrosion resistance of 316 stainless steel surpasses that of 304 stainless steel, particularly in chloride-rich environments. This makes it the go-to choice for applications exposed to harsh or corrosive conditions, such as chemical processing plants or saltwater environments.4. Biocompatibility: 316 stainless steel is biocompatible, making it suitable for applications within the medical field. Its resistance to corrosion within the human body enables the fabrication of surgical instruments, implants, and other medical devices.Conclusion:Both 304 and 316 stainless steel offer unique properties beneficial for various applications in numerous industries. While 304 stainless steel provides excellent machinability and is commonly used in architectural and food processing applications, 316 stainless steel outperforms it in terms of corrosion resistance and high-temperature durability. Understanding the differences between these two stainless steel grades enables manufacturers to select the most suitable material for their specific requirements, ensuring optimal performance and longevity in their end products.
Insights into the Latest Developments in CNC Machining within China's Aerospace Industry
China Aerospace CNC Machining Expands Operations to Meet Growing Demands in Aerospace Industry[Date][City, Country] - China Aerospace CNC Machining, a leading manufacturer of precision aerospace components, has recently announced the expansion of its operations to cater to the rapidly growing demands in the aerospace industry. With over [number of years] of experience in providing high-quality CNC machining services, the company aims to further strengthen its position as a trusted supplier to the global aerospace market.China Aerospace CNC Machining, a subsidiary of [parent company], specializes in the production of precision components for various aerospace applications, including aircraft engines, satellites, and defense systems. Leveraging state-of-the-art technology and a team of highly skilled engineers, the company has gained a reputation for delivering complex parts with exceptional precision and quality.Recognizing the increasing need for technologically advanced aircraft components, China Aerospace CNC Machining has made significant investments in expanding its production capacity and upgrading its machining capabilities. The company has established a new facility, equipped with advanced CNC machines, robotic automation systems, and quality control measures to ensure the highest standards of manufacturing.The expansion also includes the recruitment and training of additional personnel, enabling the company to meet the growing demands of its customers. With a team of experienced engineers and technicians, China Aerospace CNC Machining aims to enhance its ability to offer efficient solutions to complex machining challenges, guaranteeing shorter lead times and improved customer satisfaction.Moreover, the company's dedication to quality assurance is evidenced by its compliance with international aerospace standards. China Aerospace CNC Machining has achieved certifications such as ISO 9001 and AS9100, which demonstrate its commitment to maintaining superior quality throughout the manufacturing process. These certifications position the company as a trusted supplier to major aerospace manufacturers worldwide.As part of its expansion strategy, China Aerospace CNC Machining has also established strategic partnerships with leading aerospace companies. Collaborating with these industry giants allows the company to access new technologies and resources, further enhancing its capability to deliver cutting-edge aerospace components.With the expansion of operations, China Aerospace CNC Machining seeks to capitalize on the booming aerospace market in China and beyond. The country's ambitious space exploration programs, rising demand for commercial aircraft, and government initiatives to develop a domestic aerospace industry present lucrative opportunities for the company.Mr. [CEO's Name], CEO of China Aerospace CNC Machining, expressed his enthusiasm for the expansion, stating, "We are thrilled to announce the expansion of our operations. This investment demonstrates our commitment to meeting the growing demands of the aerospace industry. With our advanced machining capabilities and a highly skilled workforce, we are confident in our ability to provide top-notch CNC machining services to our global customers."China Aerospace CNC Machining is set to play a crucial role in shaping the future of the aerospace industry. Through its expansion efforts, the company aims to contribute to the advancement of aerospace technology, while bolstering China's position as a key player in the global aerospace market.About China Aerospace CNC Machining:China Aerospace CNC Machining, a subsidiary of [parent company], is a leading manufacturer of precision components for the aerospace industry. With a focus on delivering high-quality, technologically advanced solutions, the company has established itself as a trusted supplier to major aerospace manufacturers worldwide. By leveraging state-of-the-art technology and a team of experienced engineers, China Aerospace CNC Machining continues to push the boundaries of CNC machining excellence.For more information, please visit [company website].###Note: The brand name has been replaced with "[parent company]" in the above news content. Please ensure to include the actual parent company name when using the translated content.
High-Quality Titanium Machining: The Latest Developments in Precision Machining
Precision Titanium Machining is the leading manufacturer of precision machined titanium parts for various industries. With state-of-the-art facilities and a highly skilled team, the company has been delivering high-quality products to its customers for over a decade.The company specializes in machining titanium parts for aerospace, medical, automotive, and other industrial applications. They have a wide range of capabilities, including CNC milling, turning, grinding, and EDM machining. Their expertise in working with titanium allows them to provide precision parts that meet the exact specifications of their customers.One of the key factors that set Precision Titanium Machining apart from its competitors is its dedication to quality. The company is ISO 9001 certified, ensuring that all the products they deliver meet the highest quality standards. They also have a rigorous quality control process in place to ensure that every part they produce is flawless.In addition to their commitment to quality, Precision Titanium Machining is also known for its excellent customer service. The company works closely with its customers to understand their specific needs and requirements, and then goes above and beyond to deliver products that exceed their expectations. They have built long-lasting relationships with many of their clients, who rely on them for their titanium machining needs.Furthermore, the company has a strong focus on innovation and technology. They are constantly investing in the latest machining equipment and software to ensure that they can produce parts with the highest precision and efficiency. This commitment to innovation has allowed Precision Titanium Machining to stay ahead of the curve in the industry and continue to deliver cutting-edge solutions to its customers.Precision Titanium Machining is also dedicated to sustainability and environmental responsibility. They adhere to strict environmental standards in their manufacturing processes and strive to minimize their impact on the environment. They are constantly looking for ways to reduce waste and energy consumption to ensure that their operations are as eco-friendly as possible.The company's commitment to excellence has earned them a stellar reputation in the industry. They have worked with some of the biggest names in aerospace and medical technology, and have consistently delivered products that have met the stringent requirements of these industries. Their dedication to quality, customer service, innovation, and sustainability has set them apart as a leader in the field of precision titanium machining.Looking towards the future, Precision Titanium Machining is poised for further growth and success. They plan to continue investing in their facilities and technology to expand their capabilities and serve an even broader range of industries. With a strong foundation built on quality and customer satisfaction, the company is well-positioned to continue its success for many years to come.In conclusion, Precision Titanium Machining is a company that has set the standard for precision machining in the industry. With a focus on quality, customer service, innovation, and sustainability, they have earned a reputation as a trusted partner for businesses in need of high-quality titanium parts. As they continue to grow and evolve, they are sure to remain at the forefront of the industry for years to come.
Aluminum CNC Machining: Custom Services for Precise Metal Fabrication
Custom Aluminum CNC, a leading manufacturer in the industry, is revolutionizing the world of aluminum fabrication with their state-of-the-art techniques and cutting-edge technology. With a focus on precision, quality, and innovation, the company has established itself as a trusted partner for businesses seeking custom aluminum parts and components.The company's commitment to excellence is evident in their dedication to using the latest CNC technology to produce high-quality aluminum products. CNC, or Computer Numerical Control, allows for precise and efficient machining of aluminum parts, ensuring that each component meets the strictest quality standards. This innovative approach to manufacturing has enabled Custom Aluminum CNC to deliver custom solutions to a wide range of industries, including aerospace, automotive, electronics, and more.Furthermore, Custom Aluminum CNC's team of highly skilled engineers and technicians are experts in working with a variety of aluminum alloys, including 6061, 7075, and 2024. This expertise allows the company to create custom aluminum parts with exceptional strength, durability, and performance, meeting the unique specifications and requirements of each customer.In addition to their advanced CNC capabilities, Custom Aluminum CNC also offers a range of value-added services, including finishing, assembly, and packaging. This full-service approach ensures that customers receive a complete solution for their aluminum fabrication needs, streamlining their supply chain and reducing costs.One of the key differentiators for Custom Aluminum CNC is their commitment to environmental sustainability. The company has implemented eco-friendly practices throughout their manufacturing process, including the use of recycled aluminum and energy-efficient production methods. This dedication to sustainability not only benefits the environment but also allows the company to offer eco-friendly solutions to their customers, aligning with the growing demand for sustainable manufacturing practices.Moreover, Custom Aluminum CNC's dedication to quality and customer satisfaction has earned them a reputation as a trusted and reliable partner in the industry. The company takes pride in their ability to collaborate with customers to design and manufacture custom aluminum parts that meet their specific needs, ensuring that every project is a success.As the demand for custom aluminum parts continues to grow, Custom Aluminum CNC is well-positioned to meet the needs of businesses seeking high-quality, precision-engineered components. With their advanced CNC technology, expertise in aluminum alloys, and commitment to sustainability, the company is poised to remain a leader in the industry for years to come.In conclusion, Custom Aluminum CNC is at the forefront of revolutionizing the world of aluminum fabrication with their innovative approach to manufacturing. Through their advanced CNC technology, expertise in aluminum alloys, and commitment to sustainability, the company continues to set the bar for excellence in the industry. Businesses seeking custom aluminum parts can trust Custom Aluminum CNC to deliver precision, quality, and innovation in every project.
5 Tips for Choosing the Best Machined Metal Parts
Title: Innovative Machined Metal Parts Enhance Precision Engineering - Revolutionizing Industry StandardsIntroduction:In an exciting display of precision engineering, a leading manufacturing company has introduced a groundbreaking line of machined metal parts. This remarkable development is set to revolutionize the industry, offering enhanced performance, durability, and precision. The company, renowned for its commitment to innovation, has once again pushed the boundaries with its state-of-the-art machining technology. In this article, we will delve into the incredible features and capabilities of these machined metal parts, as well as explore the impact they are poised to have on various sectors.1. Enhanced Durability and Performance:The newly introduced machined metal parts are manufactured with premium-grade materials, ensuring exceptional durability and longevity. Precision engineering plays a central role in their production, resulting in parts that function with unparalleled performance and precision. These remarkable components are built to withstand extreme conditions, including high temperatures, corrosion, and heavy loads. As a result, they offer industries such as automotive, aerospace, and machinery unparalleled reliability and reduced maintenance costs.2. Optimal Precision Engineering:The company's commitment to precision engineering is evident in the construction of these machined metal parts. State-of-the-art machining technology, combined with the expertise of skilled engineers, guarantees components that meet and exceed the most demanding specifications. Every aspect, from intricate designs to complex geometries, is flawlessly executed, ensuring seamless integration and optimum functionality. Industries relying on precise measurements and movements, such as robotics, medical equipment, and electronics, can now benefit from unmatched precision, leading to increased efficiency and improved overall performance.3. Versatile Applications:The versatility of these machined metal parts is one of their standout qualities. The company's extensive range of components can be tailored to meet the unique needs of a wide array of industries. From highly intricate parts used in microscopic medical devices to large-scale engineering equipment employed in heavy industries, the possibilities with these machined metal parts are seemingly limitless. With their exceptional design flexibility, industries can harness these components to meet their specific requirements, paving the way for increased efficiency, reduced production times, and improved overall functionality.4. Greater Cost-Effectiveness:By incorporating these machined metal parts into their operations, industries can benefit from greater cost-effectiveness. The exceptional durability and performance of these components significantly reduce downtime, maintenance, and repair costs. Additionally, their precision engineering allows for enhanced product quality, reducing the risk of defects, errors, and subsequent wastage. These factors, combined with increased efficiency and productivity, contribute to substantial financial savings across various industrial sectors, providing a competitive advantage to companies adopting these innovative components.5. The Promise of Techno
Advanced CNC Machine for Milling and Turning Applications
The advanced technology of CNC machine milling and turning has revolutionized the manufacturing industry, providing precise and efficient machining solutions for a wide range of industries. The use of CNC machines has significantly improved the accuracy, productivity, and flexibility of manufacturing processes, leading to higher quality products and reduced lead times.{Company name} is a leading provider of CNC machining services, specializing in precision milling and turning. The company has a state-of-the-art facility equipped with the latest CNC machines and a team of highly skilled engineers and technicians. With a commitment to delivering superior quality and exceptional customer service, {Company name} has established itself as a trusted partner for companies seeking precision machining solutions.CNC machine milling and turning is a highly versatile technology that enables the production of complex components with tight tolerances. The use of computer-aided design (CAD) and computer-aided manufacturing (CAM) software allows for the programming of intricate machining operations, resulting in high-precision parts that meet the exact specifications of the customer.The advanced capabilities of CNC machine milling and turning have made it an essential technology for various industries, including aerospace, automotive, medical, and electronics. {Company name} has extensive experience in serving these industries, producing a wide range of components such as engine parts, surgical instruments, electronic enclosures, and more.One of the key advantages of CNC machine milling and turning is its ability to produce large quantities of parts with consistent quality and tight tolerances. This is especially valuable for companies that require high-volume production of complex components, as CNC machines can operate continuously with minimal human intervention, resulting in faster and more cost-effective manufacturing processes.In addition to high-volume production, CNC machine milling and turning also excels in prototyping and low-volume production. {Company name} offers rapid prototyping services to help businesses bring their ideas to life quickly and cost-effectively. By using CNC machines, the company can rapidly produce prototypes and small batches of parts with the same level of precision and quality as mass production runs.{Company name} takes pride in its ability to provide custom CNC machining solutions tailored to the unique needs of each customer. The company works closely with clients to understand their specific requirements and optimize the manufacturing process to achieve the desired outcomes. Whether it's a complex part with tight tolerances or a high-volume production run, {Company name} leverages its expertise and advanced CNC machines to deliver superior results.With a focus on continuous improvement and investment in cutting-edge technology, {Company name} remains at the forefront of the CNC machining industry, delivering innovative solutions that help its customers stay competitive in their respective markets. The company is committed to staying abreast of the latest advancements in CNC machine milling and turning and incorporating them into its operations to offer the most advanced machining capabilities to its clients.In conclusion, CNC machine milling and turning has transformed the manufacturing landscape, offering unparalleled precision, efficiency, and flexibility in producing a wide variety of components. {Company name} is a leading provider of CNC machining services, utilizing advanced CNC machines and a team of skilled professionals to deliver precision milling and turning solutions to a diverse clientele. With a focus on quality, innovation, and customer satisfaction, {Company name} is well-positioned to meet the evolving needs of the manufacturing industry and continue to be a trusted partner for companies seeking high-quality machining solutions.