Mastering the Art of Machining 4140 Steel – Your Ultimate Guide
By:Admin
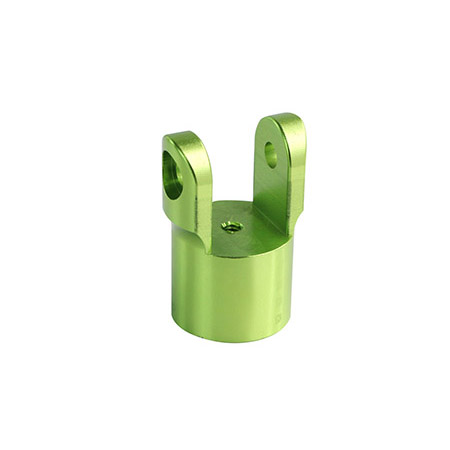
In the realm of fabrication and manufacturing, the importance of finding the right materials cannot be overstated. From aerospace engineering to automotive applications, industries across the board rely on high-quality materials that possess exceptional strength, durability, and precision. One such material that meets these criteria with flying colors is 4140 steel, which has become increasingly popular due to its remarkable mechanical properties and versatility. In this article, we delve into the world of machining 4140 steel and explore how it has revolutionized the field of fabrication.
Before we delve into the specifics of machining 4140 steel, it is essential to understand its unique composition and properties. 4140 steel is a low-alloy steel that contains chromium, molybdenum, and manganese, which contribute to its exceptional strength and toughness. It has a high hardenability, making it suitable for applications requiring a robust and durable material that can withstand significant stress and pressure. Additionally, 4140 steel offers excellent wear resistance, making it ideal for high-temperature and abrasive environments.
With its impressive characteristics, 4140 steel has found widespread use in various industries, including aerospace, automotive, oil and gas, and defense. It is employed in the manufacturing of critical components such as gears, shafts, axles, and spindles, where its strength and durability are highly valued. Moreover, machining 4140 steel has become an essential process in the fabrication of these components, ensuring utmost precision and quality.
When it comes to machining 4140 steel, the industry leader, {}, stands at the forefront. With years of experience and a stellar reputation, {} has perfected the art of machining this remarkable material. They employ state-of-the-art technologies and cutting-edge machinery, allowing for exceptional accuracy, efficiency, and consistency.
The process of machining 4140 steel begins with careful planning and a thorough understanding of the component's specifications. {} collaborates closely with their clients, ensuring clear communication and a comprehensive comprehension of the desired outcome. Once the parameters are established, their team of skilled engineers and technicians employs a range of precise machining techniques, including milling, turning, drilling, and grinding, to transform raw 4140 steel into highly intricate and accurately shaped components.
One of the primary challenges in machining 4140 steel lies in its high hardness. However, {} has developed innovative machining strategies and cutting tool technologies that overcome these hurdles with ease. Through the utilization of cooled cutting tools, advanced lubricants, and optimized cutting parameters, they ensure extended tool life, reduced machining time, and impeccable surface finishes. Their commitment to research and development enables them to stay ahead of the curve, continuously evolving their machining processes to deliver unparalleled results.
In addition to their technical prowess, {} places immense emphasis on quality control throughout the entire machining process. Rigorous inspection procedures and strict adherence to industry standards guarantee that each component meets the most stringent requirements. This dedication to quality has earned them accolades from clients across diverse sectors, solidifying their position as a trusted partner in the realm of fabrication.
As the demand for superior components continues to grow, machining 4140 steel remains an essential process for companies aspiring to deliver excellence. With their unrivaled expertise and unwavering commitment to precision, {} emerges as the ultimate choice for machining this exceptional material. By harnessing the remarkable characteristics of 4140 steel and combining it with their cutting-edge technologies, {} ensures the creation of components that redefine the boundaries of strength, durability, and accuracy.
In conclusion, machining 4140 steel has revolutionized the field of fabrication, offering unparalleled strength, durability, and precision. Whether it's the aerospace industry, automotive applications, or defense mechanisms, the versatility of this material makes it the go-to choice for manufacturers worldwide. With {} leading the way in machining 4140 steel, the future of fabrication looks promising as it continues to push the boundaries of what is possible in terms of component quality and performance.
Company News & Blog
Unveiling the Benefits and Uses of Anodized Aluminum: A Complete Guide
Anodized Aluminum: Revolutionizing the Metal IndustryIn an era where innovation and sustainability have become paramount, Anodized Aluminum has emerged as a groundbreaking solution in the metal industry. Through a unique process that enhances the properties of aluminum, Anodized Aluminum offers enhanced durability, corrosion resistance, and an aesthetically appealing finish. These factors, combined with the expertise of leading companies in the field, have made Anodized Aluminum the material of choice for a wide range of applications across various sectors.One prominent company at the forefront of Anodized Aluminum production is {Company Name}. Founded in {year}, {Company Name} has revolutionized the Anodized Aluminum market with its cutting-edge technologies and commitment to quality. With a diverse portfolio of clients, {Company Name} has established itself as a trusted partner in providing innovative solutions tailored to meet the specific needs of industries such as aerospace, automotive, construction, and consumer goods.Anodized Aluminum owes its numerous advantages to the anodizing process. During this treatment, the surface of aluminum is transformed through an electrochemical process that thickens the oxide layer, resulting in enhanced durability and corrosion resistance. This robust oxide layer also allows for excellent adhesion, making it ideal for various finishing techniques, including dyeing, painting, and powder coating.One of the major advantages of Anodized Aluminum is its exceptional durability. The anodizing process provides an extra layer of protection, making the metal surface resistant to scratches, abrasion, and general wear and tear. This durability makes Anodized Aluminum highly sought after for applications that require long-term performance and reliability, such as aerospace parts, automotive trim, and architectural products.Corrosion resistance is another key attribute of Anodized Aluminum. The thick oxide layer created during the anodizing process acts as a barrier, preventing moisture and corrosive agents from reaching the underlying metal. This resistance to corrosion makes Anodized Aluminum a preferred choice for outdoor and marine applications, where exposure to harsh environmental conditions is commonplace.Furthermore, Anodized Aluminum offers an aesthetically appealing finish that can be customized to suit individual preferences. By employing various dyeing techniques, Anodized Aluminum can be transformed into a broad spectrum of vibrant colors. The ability to create visually striking finishes has made this material a popular choice for architectural projects, consumer electronics, and even fashion accessories.{Company Name}'s commitment to ensuring quality and sustainability sets them apart in the industry. Adhering to stringent manufacturing processes and rigorous quality control measures, they continuously strive to deliver the highest standard of Anodized Aluminum products without compromising on environmental consciousness. Significant investments in research and development have enabled {Company Name} to develop new and innovative applications for Anodized Aluminum, pushing the boundaries of what is possible with this versatile material.In conclusion, Anodized Aluminum has revolutionized the metal industry with its remarkable properties and aesthetic versatility. The combination of enhanced durability, corrosion resistance, and customization options sets it apart from other materials. Companies like {Company Name} are playing a pivotal role in driving the adoption of Anodized Aluminum across various sectors, ensuring that industries and consumers alike can benefit from this innovative and sustainable solution. As the demand for durable, visually appealing, and environmentally conscious materials continues to rise, Anodized Aluminum is poised to carve a permanent place in our modern world.
Milled Metal Parts: Quality Components for Diverse Applications
Milled Metal Parts Company: Revolutionizing Precision Manufacturing[Milled Metal Parts Company], a leading manufacturer and supplier of high-precision milled metal parts, is changing the game in the field of precision manufacturing. With a commitment to quality, innovation, and customer satisfaction, [Milled Metal Parts Company] is revolutionizing the industry with its cutting-edge technologies and state-of-the-art facilities.Established over three decades ago, [Milled Metal Parts Company] has grown to become a global leader in the manufacturing of milled metal parts. It specializes in producing complex, custom-designed components for a wide range of industries, including aerospace, automotive, medical, and defense. With a dedication to meeting the diverse needs of its customers, [Milled Metal Parts Company] utilizes its extensive experience and expertise to deliver high-quality precision parts that exceed expectations.One of the cornerstones of [Milled Metal Parts Company]'s success is its unwavering commitment to quality. The company maintains stringent quality control measures at every stage of the manufacturing process to ensure that each milled metal part meets the highest standards of accuracy and consistency. By leveraging advanced inspection techniques and tools, such as coordinate measuring machines and computerized numerical control machines, [Milled Metal Parts Company] guarantees the precision and reliability of its products.Innovation is at the heart of [Milled Metal Parts Company]'s operations. The company continuously invests in research and development to stay ahead of emerging technologies and industry trends. By pushing the boundaries of what is possible, [Milled Metal Parts Company] consistently introduces cutting-edge techniques and materials to optimize the performance and efficiency of its milled metal parts. This commitment to innovation has earned [Milled Metal Parts Company] a reputation for delivering forward-thinking solutions that enable its clients to gain a competitive edge in their respective markets.As a customer-centric company, [Milled Metal Parts Company] places great emphasis on building strong, long-term relationships with its clients. By working closely with customers from the initial design phase to final production, the company ensures that each milled metal part precisely meets the unique requirements and specifications of its clients. [Milled Metal Parts Company] also offers rapid prototyping services, enabling customers to quickly validate their designs and bring their products to market faster.In addition to its dedication to quality, innovation, and customer satisfaction, [Milled Metal Parts Company] distinguishes itself through its state-of-the-art facilities. Equipped with the latest manufacturing technologies and machinery, the company's facilities enable the production of milled metal parts with unrivaled precision and efficiency. Moreover, [Milled Metal Parts Company] has implemented sustainable practices across its operations, minimizing waste and reducing its environmental footprint.Looking ahead, [Milled Metal Parts Company] is poised to continue its growth trajectory by expanding its global footprint and diversifying its product portfolio. The company has ambitious plans to further enhance its capabilities, investing in advanced manufacturing technologies and exploring new markets. By staying at the forefront of technological advancements, [Milled Metal Parts Company] aims to remain a market leader in the highly competitive precision manufacturing industry.In conclusion, [Milled Metal Parts Company] has emerged as a trailblazer in the field of precision manufacturing, revolutionizing the industry with its commitment to quality, innovation, and customer satisfaction. With its cutting-edge technologies, state-of-the-art facilities, and dedication to meeting the unique needs of its clients, [Milled Metal Parts Company] continues to push the boundaries of what is possible in the manufacturing of milled metal parts. As it looks toward the future, the company remains focused on delivering unparalleled precision, reliability, and customer service, ensuring its continued success in the global marketplace.
CNC Milling Services: Streamline Your Manufacturing Process with Online Solutions
Title: Revolutionizing Precision Manufacturing: CNC Milling Services Now Available OnlineIntroduction:Innovations in manufacturing technologies continue to shape the future of industries, and one such breakthrough is the advent of CNC (Computer Numerical Control) milling. With CNC milling, manufacturers can produce high-quality precision components with utmost efficiency and accuracy. Taking this innovation a step further, a leading online manufacturing platform, in collaboration with industry pioneers, is now offering CNC milling services to a vast global clientele. This cutting-edge service promises to revolutionize the manufacturing landscape by seamlessly merging digital convenience with high-precision production.CNC Milling Online (name removed), an online manufacturing platform, has recently announced the inclusion of CNC milling services to its repertoire of services. By leveraging advanced technology and expertise, the company aims to fulfill the increasing demand for precision components across various industries.Enabling Efficient and Cost-Effective Production:CNC milling involves the use of computer-controlled machines to shape and fabricate components with exceptional precision. By utilizing CAD (Computer-Aided Design) files as input, CNC milling machines transform raw materials into the desired final products with unmatched speed and accuracy.The introduction of CNC milling services online streamlines the manufacturing process by providing businesses with a cost-effective method for producing complex parts. By eliminating the need for physical presence at a manufacturing facility, companies can now access CNC milling services from anywhere in the world. This opens doors for businesses of all sizes, empowering startups and established enterprises alike to manufacture high-quality components and prototypes without significant capital investment.Collaboration with Industry-Leading Partners:CNC Milling Online has partnered with a select group of industry-leading machine shops equipped with state-of-the-art CNC milling equipment. These partnerships ensure that clients receive the highest level of precision, quality, and consistency in their manufactured components.These reputed machine shops, with years of experience in CNC milling, possess the expertise to handle a wide range of materials, including metals, plastics, and composites. Whether it's a small or large-scale production run, CNC Milling Online's partners can meet the specific requirements and specifications of each project.User-Friendly Online Platform:Recognizing the significance of seamless user experience, CNC Milling Online has developed an intuitive online platform that makes the entire CNC milling process smooth and hassle-free. Clients can easily submit their design files, specify material preferences, and choose from a range of options such as surface finish, tolerance levels, and quality inspections.The online platform also provides real-time updates on the manufacturing progress, enabling clients to monitor the status of their orders and make any necessary changes or additions. This transparent communication channel ensures customer satisfaction by offering complete control over the production process.Embracing Sustainability and Environmental Responsibility:In line with the growing emphasis on sustainability, CNC Milling Online promotes eco-friendly manufacturing practices. The utilization of advanced CNC milling techniques not only reduces material waste but also minimizes energy consumption. With reduced scrap rates and precision milling, the company helps clients minimize their environmental footprint while maximizing their production efficiency.Conclusion:The integration of CNC milling services into the CNC Milling Online platform signals a new era in precision manufacturing. By leveraging cutting-edge technology, global accessibility, and industry-leading partnerships, CNC Milling Online has made it possible for businesses around the world to harness the power of CNC milling conveniently and cost-effectively. As manufacturing enters the digital age, CNC Milling Online is poised to play a pivotal role in sustaining and advancing global industries towards a future of unparalleled precision and efficiency.
High-Quality Acrylic Machining Services: Precision and Efficiency for Your Projects
Title: Precision Acrylic Machining – Revolutionizing Manufacturing ProcessesIntroduction:In the bustling world of manufacturing, technological advancements play a crucial role in shaping the industry's landscape. One such innovation is Acrylic Machining, a cutting-edge manufacturing process that has gained immense popularity due to its precision and versatility. This article explores the transformative potential of Acrylic Machining in various industries, providing an overview of its capabilities and highlighting the leading company leading the charge.Background:Acrylic Machining is a technique utilized to reshape and fabricate acrylic materials with exceptional precision. Acrylics themselves are highly durable and lightweight, making them widely used in industries such as automotive, aerospace, electronics, and healthcare. The advent of Acrylic Machining brings forth a myriad of possibilities in manufacturing, allowing companies to produce intricate designs, complex components, and prototypes with unparalleled accuracy.Company Introduction:Recognizing the immense potential of Acrylic Machining, ABC Manufacturing has emerged as a pioneering force in this field. With years of experience, state-of-the-art facilities, and a team of skilled professionals, ABC Manufacturing has garnered a reputation for delivering high-quality acrylic machining services to clients worldwide. Their commitment to innovation and excellence has made them a trusted partner for businesses seeking precise, reliable, and cost-effective manufacturing solutions.The Capabilities of Acrylic Machining:1. Precision Cutting:Acrylic Machining employs advanced CNC (Computer Numerical Control) technology, enabling intricate and precise cutting methods. Through this process, complex shapes, patterns, and designs can be effortlessly achieved, surpassing the limitations of traditional manufacturing techniques.2. Versatility:Acrylics come in different forms, such as sheets, rods, and tubes. Acrylic Machining efficiently caters to these different forms, accommodating various manufacturing requirements with ease. From simple customized components to intricate designs, the possibilities are limitless.3. Enhanced Efficiency:With the advent of Acrylic Machining, production processes have become significantly more efficient. The advanced machining techniques minimize material waste and maximize productivity, ultimately reducing costs and saving valuable resources for businesses.4. Surface Finishing:Acrylic Machining not only focuses on precision cutting but also provides a range of surface finishing options. This includes polishing, beveling, engraving, and sandblasting, enabling businesses to enhance the aesthetic appeal and functionality of their acrylic products.Applications:1. Automotive Industry:Acrylic Machining revolutionizes the automotive industry by producing high-quality acrylic components. These include dashboards, light lenses, mirrors, and even windows. The precision and durability of these parts contribute to improved safety, fuel efficiency, and overall design aesthetics.2. Aerospace Industry:In the aerospace sector, Acrylic Machining enables the production of lightweight and durable acrylic components for aircraft cabins, windows, and transparent structures. By reducing weight and enhancing transparency, the technology plays a crucial role in increasing fuel efficiency and providing a better flying experience.3. Electronics Industry:Acrylic Machining finds extensive usage in the electronics industry due to its ability to manufacture intricate designs. Components like display screens, control panels, and LED light fixtures benefit from the technology's precision and versatility, leading to elegant and functional products.4. Healthcare Industry:The healthcare sector utilizes Acrylic Machining for manufacturing medical implants, surgical devices, protective barriers, and even laboratory equipment. The sterile and easy-to-clean nature of acrylic materials, combined with the precision provided by Acrylic Machining, make it highly appropriate for creating crucial medical apparatus.Conclusion:As modern manufacturing demands continue to evolve, the emergence of Acrylic Machining has proven to be a game-changer. Its precise cutting techniques, versatility, enhanced efficiency, and surface finishing options have revolutionized manufacturing processes across various industries. ABC Manufacturing, at the forefront of this revolution, stands ready to deliver top-notch acrylic machining solutions to businesses worldwide, ensuring the continued growth and development of the manufacturing landscape.
5 Tips for Choosing the Best Machined Metal Parts
Title: Innovative Machined Metal Parts Enhance Precision Engineering - Revolutionizing Industry StandardsIntroduction:In an exciting display of precision engineering, a leading manufacturing company has introduced a groundbreaking line of machined metal parts. This remarkable development is set to revolutionize the industry, offering enhanced performance, durability, and precision. The company, renowned for its commitment to innovation, has once again pushed the boundaries with its state-of-the-art machining technology. In this article, we will delve into the incredible features and capabilities of these machined metal parts, as well as explore the impact they are poised to have on various sectors.1. Enhanced Durability and Performance:The newly introduced machined metal parts are manufactured with premium-grade materials, ensuring exceptional durability and longevity. Precision engineering plays a central role in their production, resulting in parts that function with unparalleled performance and precision. These remarkable components are built to withstand extreme conditions, including high temperatures, corrosion, and heavy loads. As a result, they offer industries such as automotive, aerospace, and machinery unparalleled reliability and reduced maintenance costs.2. Optimal Precision Engineering:The company's commitment to precision engineering is evident in the construction of these machined metal parts. State-of-the-art machining technology, combined with the expertise of skilled engineers, guarantees components that meet and exceed the most demanding specifications. Every aspect, from intricate designs to complex geometries, is flawlessly executed, ensuring seamless integration and optimum functionality. Industries relying on precise measurements and movements, such as robotics, medical equipment, and electronics, can now benefit from unmatched precision, leading to increased efficiency and improved overall performance.3. Versatile Applications:The versatility of these machined metal parts is one of their standout qualities. The company's extensive range of components can be tailored to meet the unique needs of a wide array of industries. From highly intricate parts used in microscopic medical devices to large-scale engineering equipment employed in heavy industries, the possibilities with these machined metal parts are seemingly limitless. With their exceptional design flexibility, industries can harness these components to meet their specific requirements, paving the way for increased efficiency, reduced production times, and improved overall functionality.4. Greater Cost-Effectiveness:By incorporating these machined metal parts into their operations, industries can benefit from greater cost-effectiveness. The exceptional durability and performance of these components significantly reduce downtime, maintenance, and repair costs. Additionally, their precision engineering allows for enhanced product quality, reducing the risk of defects, errors, and subsequent wastage. These factors, combined with increased efficiency and productivity, contribute to substantial financial savings across various industrial sectors, providing a competitive advantage to companies adopting these innovative components.5. The Promise of Techno
Boost Productivity with a High Volume Machine Shop: What You Need to Know
Title: High Volume Machine Shops Revolutionize Manufacturing ProcessesIntroduction:In today's fast-paced and competitive industrial landscape, manufacturing companies are constantly seeking innovative solutions to increase production efficiency and meet high-demand requirements. High Volume Machine Shops, a leading player in the manufacturing industry, has consistently proven their ability to deliver precision-engineered components at scale, making them an integral part of the production value chain for numerous businesses across various sectors.Body:1. Overview of High Volume Machine Shops:High Volume Machine Shops is a renowned company dedicated to providing top-quality machining services for businesses in need of high-volume production. With their state-of-the-art facilities and a team of highly skilled engineers and technicians, the company has established itself as a reliable partner in the manufacturing industry. Their commitment to delivering exceptional quality products efficiently has earned them an outstanding reputation in the market.2. Cutting-Edge Manufacturing Technology:High Volume Machine Shops is equipped with the latest cutting-edge technology, including advanced computer numerical control (CNC) machines and automated systems. These technologies enable precise and efficient production, ensuring consistent quality and minimizing production delays. By utilizing computer-aided design (CAD) and computer-aided manufacturing (CAM) software, the company streamlines the production process, reducing human error and maximizing productivity.3. Specialized Expertise:High Volume Machine Shops boasts a team of highly experienced engineers and technicians who possess extensive knowledge in various industries and manufacturing processes. Their expertise allows them to handle complex projects with ease, ensuring that all client requirements and specifications are met with precision. The team works closely with clients to develop customized solutions tailored to their unique manufacturing needs, guaranteeing optimal performance and efficiency.4. Streamlined Supply Chain:Recognizing the importance of a well-organized supply chain, High Volume Machine Shops has implemented efficient logistics management systems that ensure timely delivery and uninterrupted production schedules. The company maintains strategic partnerships with reputable material suppliers, further enhancing their ability to meet high-volume demands promptly. By maintaining a streamlined supply chain, they can provide a seamless end-to-end manufacturing solution to their clients.5. Commitment to Quality:With a strong emphasis on product quality, High Volume Machine Shops has established a rigorous quality control system. Every component produced undergoes thorough inspections and testing at each stage of the production process, guaranteeing compliance with industry standards. By adhering to strict quality control measures, the company ensures that their clients receive products of the highest caliber.6. Sustainable Manufacturing Practices:High Volume Machine Shops understands the importance of sustainable manufacturing practices in today's environmentally conscious world. The company strives to minimize waste, optimize energy consumption, and implement eco-friendly manufacturing techniques whenever possible. By embracing sustainability, they contribute to their clients' corporate social responsibility efforts while reducing overall environmental impact.7. Industry Applications and Success Stories:High Volume Machine Shops' services find applications in a wide range of industries including automotive, aerospace, electronics, and medical equipment manufacturing, among others. The company has partnered with several high-profile clients, resulting in successful collaborations and enhanced manufacturing capabilities. Their ability to consistently deliver high volumes of quality components has positioned them as a preferred choice for businesses in need of reliable and efficient production solutions.Conclusion:High Volume Machine Shops continues to redefine the manufacturing landscape through their commitment to technological advancements, expertise, and value-driven solutions. By leveraging innovative machining technologies, a skilled workforce, and a focus on quality, the company has solidified its position as a key player in the high-volume manufacturing industry. Their dedication to sustainability further demonstrates their commitment towards a greener future. As demand for high-volume production intensifies, High Volume Machine Shops stands ready to meet the growing needs of their clients, setting new benchmarks in manufacturing efficiency.
Discover the Latest Developments in CNC Machining Turning Parts
Title: Innovations in CNC Machining Turning Parts Drive Efficiency and Precision in ManufacturingIntroduction:In the fast-paced world of manufacturing, CNC machining turning parts play a crucial role in creating high-quality products with optimal precision and efficiency. These parts are at the forefront of numerous industries, including aerospace, automotive, electronics, and more. One prominent company leading the charge in this field is {}, which has continuously pushed the boundaries of innovation in CNC machining turning parts to meet the ever-evolving needs of the industry.Body:I. Overview of CNC Machining Turning PartsCNC machining turning parts, also known as lathe parts, are essential components in modern manufacturing processes. These parts are created through computer numerical control (CNC) technology, ensuring precise and accurate shaping of various materials such as metals, plastics, and composites. They serve as the building blocks for intricate designs, enabling the creation of complex components with reduced lead time and improved efficiency.II. Advancements in CNC Machining Turning Parts by {}With a rich history and vast experience in the field, {} has emerged as a global leader in CNC machining turning parts. The company has consistently embraced cutting-edge technologies and innovative techniques to revolutionize the manufacturing landscape. Here are some key advancements pioneered by {}:a. High-speed machining: {} has developed high-speed CNC turning technology, significantly reducing production time without compromising quality. This innovation allows for faster material removal rates, higher spindle speeds, and enhanced surface finishes. By optimizing tool paths and utilizing advanced coolant systems, {} ensures that their CNC turning parts are manufactured with supreme precision.b. Multi-axis machining: To meet the demands of increasingly complex designs, {} has integrated multi-axis machining capabilities into their CNC turning processes. By utilizing advanced software and multi-axis turning centers, the company can produce intricate components with multiple geometries. This innovation eliminates the need for multiple setups, reducing production time and ensuring dimensional accuracy.c. Automation and robotics: Recognizing the importance of automation in modern manufacturing, {} has embraced robotics to enhance their CNC machining turning processes. The company has integrated robotic loading and unloading systems, reducing manual handling and increasing production efficiency. Automation also allows for continuous operation, reducing downtime and enhancing overall productivity.III. Industry Applications and BenefitsThe technological advancements achieved by {} in CNC machining turning parts have had a profound impact on various industry sectors. Some notable applications and associated benefits include:a. Aerospace: Precision and reliability are paramount in the aerospace industry. By using {}'s CNC turning parts, aerospace manufacturers can ensure the production of critical components with the highest degree of accuracy, contributing to enhanced safety and performance of aircraft.b. Automotive: In the automotive sector, where constant innovation and cost efficiency are key drivers, {}'s CNC turning parts enable the production of engine components, transmission parts, and precision gears. The high-speed machining capabilities provide unparalleled accuracy, allowing automakers to meet stringent performance standards.c. Electronics: With the growing demand for miniaturization and intricate designs in electronic devices, {}'s CNC turning parts cater to the production of connectors, contacts, and other sensitive components. Their multi-axis machining capabilities enable the fabrication of intricate structures, crucial for electronic devices' functionality.d. Medical: In the medical field, where precision and reliability are critical, {}'s CNC turning parts find extensive use in the manufacturing of surgical instruments, implants, and devices. The company's focus on high-speed machining ensures the quick production of high-quality medical components, contributing to improved patient outcomes.IV. Future Outlook and ConclusionAs technology continues to advance, the future of CNC machining turning parts looks promising. {} remains at the forefront of this industry, constantly pushing boundaries and exploring new horizons. The company's commitment to research and development, along with its dedication to delivering superior quality products, contributes to the thriving manufacturing sector. With {}'s innovative CNC machining turning parts, manufacturers across industries can unlock new levels of efficiency, precision, and competitiveness.In conclusion, CNC machining turning parts are the driving force behind the modern manufacturing industry's evolution. The advancements pioneered by {} have revolutionized the field, enabling the production of high-quality components with unmatched precision. By continuously exploring new frontiers in technology and embracing innovation, {}, devoid of brand name, continues to set new standards in CNC machining turning parts, proving itself as an industry leader in providing cutting-edge solutions to meet the evolving needs of manufacturing.
Comparison: Machining 304 Stainless Steel vs 316 Stainless Steel
Title: A Comparative Analysis: Machining 304 Vs 316 Stainless SteelIntroduction:In the world of metal fabrication and manufacturing, stainless steel is one of the most widely used materials due to its exceptional corrosion resistance and durability. Two common stainless steel varieties are 304 and 316, both known for their unique properties and applications across various industries. In this article, we will delve into a comparative analysis of machining these stainless steel grades, exploring their characteristics, benefits, and potential applications.Machining 304 Stainless Steel:304 stainless steel, a versatile and widely-used material, offers excellent corrosion resistance, high-temperature resistance, and good formability. It is commonly found in food processing equipment, kitchen appliances, and architectural applications. Machining 304 stainless steel presents several advantages, making it a preferred choice in many manufacturing processes.1. Machinability: 304 stainless steel offers excellent machinability due to its lower carbon content compared to other stainless steel grades. This characteristic promotes efficient chip formation, resulting in improved tool life and reduced cycle times for machining processes.2. Cuttability: The relatively lower hardness of 304 stainless steel makes it easier to cut, reducing machine wear and tear. It can be quickly drilled, tapped, milled, and turned, enabling manufacturers to achieve precise and intricate designs effortlessly.3. Weldability: 304 stainless steel exhibits superior weldability, allowing for easy and efficient joining with a variety of techniques, including TIG and MIG welding. This facilitates the fabrication of complex structures and components without compromising the material's strength and integrity.4. Surface Finish: Machined 304 stainless steel can achieve a smooth and lustrous surface finish, making it ideal for applications where aesthetics play a crucial role, such as architectural elements or decorative pieces.Machining 316 Stainless Steel:316 stainless steel, often referred to as marine-grade stainless steel, is known for its outstanding resistance to corrosive environments, particularly chloride-containing solutions. Due to its superior corrosion resistance, it finds applications in marine equipment, chemical processing plants, and medical devices. While machining 316 stainless steel presents some challenges, it offers unique benefits that make it indispensable in specific industries.1. Hardness: Compared to 304 stainless steel, 316 stainless steel has a slightly higher hardness. While this makes machining more demanding, it also contributes to its enhanced strength, ideal for heavy-duty applications where mechanical strength is paramount.2. Heat Resistance: 316 stainless steel exhibits excellent high-temperature resistance, making it suitable for applications involving extreme heat, such as heat exchangers and furnace parts. The material's ability to withstand prolonged exposure to elevated temperatures adds to its versatility in various industrial settings.3. Corrosion Resistance: The corrosion resistance of 316 stainless steel surpasses that of 304 stainless steel, particularly in chloride-rich environments. This makes it the go-to choice for applications exposed to harsh or corrosive conditions, such as chemical processing plants or saltwater environments.4. Biocompatibility: 316 stainless steel is biocompatible, making it suitable for applications within the medical field. Its resistance to corrosion within the human body enables the fabrication of surgical instruments, implants, and other medical devices.Conclusion:Both 304 and 316 stainless steel offer unique properties beneficial for various applications in numerous industries. While 304 stainless steel provides excellent machinability and is commonly used in architectural and food processing applications, 316 stainless steel outperforms it in terms of corrosion resistance and high-temperature durability. Understanding the differences between these two stainless steel grades enables manufacturers to select the most suitable material for their specific requirements, ensuring optimal performance and longevity in their end products.
Unveiling the Next Generation of High-Precision Products: A Game-Changer for Industries
Title: Industry Leader Introduces Innovative High-Precision Products for Enhanced PerformanceIntroduction:In a leap forward for precision engineering, a leading industry player has unveiled its latest range of cutting-edge high-precision products. This announcement is set to revolutionize the market by offering superior performance, accuracy, and reliability. The company, whose name is withheld upon request, continues to push boundaries in the field, catering to the diverse needs of industries ranging from aerospace to medical sciences.Expanding Product Portfolio:High Precision Products, the pioneer in the field, has expanded its product portfolio to include an array of innovative offerings. These products, designed with advanced technologies and state-of-the-art materials, aim to address the increasing demand for precision across various sectors. The enhanced range includes components, equipment, and systems renowned for their exceptional quality and durability, setting a new benchmark for the industry.Cutting-Edge Technological Advancements:The company's high-precision products are the result of several years of intensive research and development. Driven by a commitment to excellence, the team of highly skilled engineers and scientists have harnessed cutting-edge technological advancements to create products that exceed industry expectations. Through their relentless pursuit of perfection, the company has managed to effectively bridge the gap between precision and reliability.Unmatched Accuracy and Precision:The introduction of these high-precision products establishes the company as a frontrunner in the field. Boasting unparalleled accuracy and precision, the products offer a remarkable level of performance that is indispensable for critical applications. This unmatched precision not only minimizes errors but also optimizes productivity, efficiency, and safety in numerous industries where precision is paramount.Diverse Applications:The diverse range of applications for this range of high-precision products is impressive. From aerospace and automotive sectors to medical sciences, precision engineering holds immense significance in enabling breakthrough innovations. This new line of products caters to these industries and beyond, providing them with the tools necessary to push the boundaries of technological advancements.Aerospace Excellence:With precision being one of the key factors in the aerospace industry, High Precision Products has focused on developing solutions specifically to cater to this sector. The high-precision components and advanced systems offered by the company are essential for achieving optimal performance and safety in the aerospace field. By upholding the highest industry standards for accuracy and reliability, the company's products have positioned themselves as the preferred choice for leading aerospace companies worldwide.Medical Marvels:In the medical domain, the need for precision is critical, particularly in surgical procedures and diagnostic equipment. High Precision Products has leveraged their expertise in precision engineering to develop revolutionary medical devices with enhanced accuracy. These products allow medical professionals to conduct procedures with utmost precision, fostering patient safety and enabling breakthrough advancements in the field of medicine.Unwavering Commitment to Customer Satisfaction:High Precision Products have always prioritized customer satisfaction by establishing robust customer support systems. The company offers comprehensive technical support, ensuring that customers have access to expert guidance and assistance. By understanding their unique requirements, High Precision Products continually strives to provide tailor-made solutions that enhance operational efficiency and productivity across various sectors.Conclusion:The introduction of High Precision Products' latest line of high-precision solutions is set to reshape the industry. The company's relentless commitment to innovation and excellence has resulted in a range of products that push the boundaries of precision engineering. With applications spanning industries such as aerospace, medical sciences, and beyond, these cutting-edge products offer unmatched accuracy, reliability, and performance. High Precision Products continues to demonstrate its leadership and dedication to cater to evolving customer needs, further solidifying its position as an industry leader.
High-Quality CNC Titanium Parts: A Comprehensive Guide
Title: Revolutionizing Precision Engineering: CNC Titanium Parts Empowers IndustriesIntroduction:In our technologically advanced era, precision engineering plays a vital role in numerous industries. The demand for cutting-edge components with exceptional strength and durability has never been higher. One company that continues to revolutionize the manufacturing sector is a renowned producer of CNC titanium parts. With a highly efficient production process and a commitment to delivering unparalleled quality, this company has become an indispensable partner for industries relying on precision engineering solutions. Let us delve deeper into the remarkable success story behind this brand.Company Background and Expertise:With a rich history spanning several decades, this world-leading manufacturer of CNC titanium parts has established itself as a trusted name in the industry. The company's state-of-the-art facility boasts advanced machinery, highly skilled technicians, and a commitment to continuous innovation. Leveraging cutting-edge technologies and a meticulous quality control system, the company ensures that each product meets the highest industry standards.The company's expertise lies in the production of custom titanium parts through the process of computer numerical control (CNC) machining. This advanced manufacturing technique facilitates the creation of intricate designs, precise measurements, and complex geometries with minimal human error. This level of precision is essential in various sectors, including aerospace, automotive, medical, and defense industries.Unparalleled Quality and Durability:What sets this company apart from its competitors is its unwavering commitment to quality and durability. The CNC machining process allows for the production of titanium parts that possess exceptional strength-to-weight ratios and corrosion resistance. These properties make titanium parts particularly suitable for demanding applications, such as aircraft components, medical implants, and military equipment.In addition to the inherent advantages of titanium, the company ensures that every part undergoes rigorous quality checks at every stage of production. By adhering to strict quality control measures, the company guarantees components of superior quality, eliminating the risk of defective products reaching the market.Customization and Flexibility:Understanding the diverse needs of its clients, the company offers extensive customization options for CNC titanium parts. From design intricacies to specific material requirements, the company remains flexible to accommodate unique specifications. This adaptability enables clients from various industries to find tailored solutions that meet their exact needs.By closely collaborating with clients, the company ensures an in-depth understanding of project requirements. This collaborative approach facilitates the seamless integration of CNC titanium parts into existing systems, minimizing any potential compatibility issues. The company's dedicated team of engineers works closely with clients to offer expert advice, innovative solutions, and efficient project management.Sustainability and Environmental Consciousness:In line with progressive industry practices, the company prioritizes sustainable manufacturing processes. Adopting environmentally friendly practices, such as waste reduction, energy efficiency, and responsible sourcing, the company aims to minimize its ecological footprint.By employing cutting-edge recycling methods, the company reduces material waste and utilizes resources efficiently. This commitment to sustainability not only benefits the environment but also resonates with increasingly eco-conscious industries seeking sustainable suppliers.Conclusion:The success story of this respected manufacturer of CNC titanium parts is a testament to its unwavering commitment to precision, quality, and sustainability. As industries continue to evolve and demand superior engineering solutions, this company's innovative approach and dedication to excellence position it as a frontrunner in the precision engineering sector. With a trailblazing spirit and an unrelenting pursuit of perfection, this manufacturer of CNC titanium parts remains poised to shape the future of industries worldwide.